Infrared Inspections to Detect Latent Moisture
Sponsored by:
Infrared Inspections to Detect Latent Moisture
As interest in building remediation has increased, thermography has become a common tool for helping to detect moisture damage. Knowing when and how to conduct an infrared inspection is key to success.
Water infiltration into buildings can have devastating effects on building materials. Left untreated, latent moisture can cause excess energy loss, mold growth and/or structural failure. Latent moisture also causes changes in the thermal capacitance and conductivity of materials.
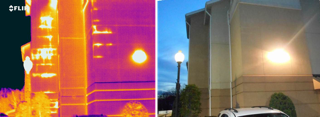
by latent moisture within EIFS clad wall. Image
taken post sunset following a sunny day.
Prior to performing an infrared inspection, determine the best vantage point for imaging. Insulated roofs and exterior building finishes such as EIFS are traditionally inspected from the exterior of the building. Interior inspections are usually effective when moisture is affecting interior finishes of the building such as drywall. Thermal imaging may not be effective for low emittance targets.
Next, choose an appropriate time to ensure that a detectable Delta T will be present. For roofs and building exteriors, best results are usually obtained during evening hours following a sunny day. As an alternative, inspections may also be performed when there is an inside/outside temperature differential of at least 10Cº. In some cases, inspections performed from the interior may be performed with a smaller Delta T.
Thermal signatures associated with latent moisture will vary with type of building material and the amount of moisture contained therein. Depending upon vantage point and time of inspection, exceptions caused by latent moisture may show as either hot or cold thermal anomalies. These anomalies may be amorphously shaped, mottled, or correspond to the size and shape of absorbent materials. All thermal data should be correlated with invasive testing to ascertain moisture content of inspected areas.
Infrared inspections of building envelopes is one of the many topics covered in the Infraspection Institute Level I Certified Infrared Thermographer® training course. For more information on class locations or our Distance Learning program, visit www.infraspection.com or call 609-239-4788.
Advertisement