Cody Jackson
Level III Certified Infrared Thermographer
JTI Services, LLC
515 South Main StreetWinthrop, MN 55396Ph: 507-647-7812www.JTIservices.com
Abstract
In most commercial facilities, an overlooked but essential asset to the facility is the electrical system. Almost everything runs on electricity and once installed, most electrical equipment is forgotten about until something burns up and stops working. Typically, electrical maintenance consists of either replacing failed equipment when it breaks down (usually very expensive) or routinely replacing old equipment with new whether it needs it or not (also expensive and wasteful). Another option available involves using infrared thermography as a way to improve electrical maintenance.
What Is Infrared Thermography?
Before learning how infrared thermography can improve electrical maintenance, we first need to know what infrared thermography is. According to Infraspection Institute – the world’s oldest independent training and certification firm for thermographers, “Infrared thermography is a non-contact, non-destructive test method that utilizes a thermal imager to detect, display, and record thermal patterns and temperatures across the surface of an object.” Infrared thermography can be applied to many industries and vocations from identifying breast cancer in medical thermography to finding construction inefficiencies during building envelope inspections.
How Can Infrared Thermography Improve Electrical Maintenance?
Since infrared thermography is a test method that detects heat patterns, the method is highly useful when applied to electrical maintenance in the form of infrared inspections. During an electrical infrared inspection, a thermographer is looking through the entire electrical system from the main switchboards down to individual disconnects and panels for odd temperature differences and patterns called anomalies. Anomalies often result from loose connections, overloaded circuits, bad circuit breakers, poorly performing fuses, etc. in an electrical system. If a facility is looking to improve their electrical maintenance program, the following are three ways infrared thermography can make that happen.
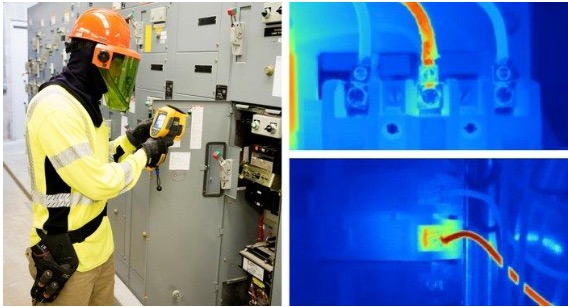
IR images of loose connections. Photo credit: JTI Services, LLC
Infrared Thermography is Non-Contact – When considering how infrared thermography could improve an electrical maintenance program, think first about the actual techniques used in infrared inspections. First and foremost, infrared thermography is a non-contact test method. Electricity can be dangerous and the less risk a maintenance electrician has to take, the better. Unlike other test methods that require contact with the target such as ultrasound or vibration analysis, infrared thermography doesn’t rely on touch. IR thermography can also help with troubleshooting electrical equipment like tripping breakers and fuses. Instead of replacing the nuisance equipment fully, an infrared inspection could reveal that loose connections are causing the problems – not that the equipment is bad, which could save the cost of full replacement.
IR Thermography can be Easily Added – Another way infrared thermography can improve electrical maintenance is by adding infrared inspections to a preventative maintenance program. A preventative maintenance program incorporates a routine schedule of cleaning, exercising, and replacing electrical equipment with the goal of preventing old equipment from causing unscheduled downtime. Infrared thermography is predictive in nature due to the fact that infrared imagers can detect heat which is a major cause of electrical equipment failure. Combined, predictive and preventative maintenance techniques both help improve electrical maintenance. Two ways to incorporate IR thermography would be to hire an infrared inspection company or buy the equipment, get training, and create the IR inspection program in-house. The good news is that once the initial investment is made for either option, the time it takes to add infrared thermography to an electrical maintenance program is minimal.
Validates ROI of Program – One of the most valuable ways in which infrared thermography improves electrical maintenance is by validating the return on investment (ROI) of the maintenance practice itself. When conducted by an experienced thermographer and followed with timely repairs, infrared inspections can provide a $4 for every $1 value of the IR inspection. Reason being, infrared inspections can catch symptoms of problems before they cause equipment failure. Correcting problems before they lead to failure ensures longer equipment life and less unexpected downtime. The cost of adding infrared thermography to an electrical maintenance program is minimal compared to the cost of equipment failure and a potential facility shutdown.
Conclusion
Electrical systems are highly reliable; however, they do require some periodic maintenance. Due to this fact, electrical maintenance programs are needed to maintain equipment throughout a facility’s lifecycle. Creating a highly efficient electrical maintenance program that extends the life of the electrical system while also maintaining a budget, is no easy task. Ask any maintenance manager, if they had a non-contact test method that was easy to add to the existing maintenance program while also providing a good ROI, would they want it? Absolutely, and infrared thermography is just that.