James Brady
Level III Certified Infrared Thermographer
Brady Infrared Inspections, Inc.
935 Pine Castle CourtStuart, FL 34996772-288-9884www.bradyinfrared.com
Abstract
Unexpected failures in a utility provider’s electrical equipment can result in lost customer minutes and damage to valuable equipment. They can also undermine consumer confidence in their power provider. Routine infrared inspections coupled with effective repairs can pay huge dividends for electrical utilities by helping to reduce unscheduled downtime. Drawing upon a database compiled from over seven years of infrared inspections of electric utility equipment, this paper will discuss common problems such as connections and lightning arrestors as well as some not so common problems associated with oil filled equipment and insulators.
Introduction
The electrical utility industry offers limitless opportunities for thermography. Most utility companies use infrared on a regular basis as part of a regimented maintenance program. Some contract out their infrared inspection needs to infrared consultants. Others have in-house programs that range from one camera that is used to periodically check equipment to full-time inspection crews that drive custom modified vans and scan equipment year-round. Whatever the size or type of program, the bottom line is infrared is a powerful tool that can identify problems quickly, accurately, and safely in the electrical utility industry.
The utility industry can be broken down into three main sectors, 1) power generation, 2) substations and switchyards, and 3) transmission and distribution. Within these three areas infrared applications abound.
Power generation plants offer infrared inspection of high and low-voltage electrical equipment, refractory lined vessels, steam driven equipment, and roof systems.
Substations and switchyards offer infrared inspection of various conductor connections, switches, oil-filled tank equipment including breakers, transformers and voltage regulators, lightning arrestors, and capacitors.
The transmission and distribution sector offers infrared inspection of overhead power line equipment ranging from lightning arrestors, transformers, breakers, switches, conductor connections, and capacitors. Also available is underground equipment, switchgear enclosures, pad mount transformers, and transformer vaults.
With over seven years of infrared scanning for various utility companies, I will present not-so-common problems associated with the three sectors of the electrical utility industry. I will also touch on a few specialized projects my company has been involved in including absolute temperature scans to inspection of specific pieces of overhead distribution equipment.
Power Generation
Power generation plants are responsible for manufacturing electricity and shipping it out along transmission lines at specified voltages designed to meet load demands and actual distances of transmission. The means by which the power is produced varies from fuel burning technologies and nuclear power to turn steam turbine, fuel burning co-generators, hydro-electric structures, and more recently solar and wind farms. Whatever the means of creating electric power, infrared applications are numerous.
Most infrared inspections focus on electrical equipment, including high and low voltage switchgear and breakers and motor control centers that operate the vast number of motor driven pumps necessary for production. Common connection problems, overloaded circuits, and failing components can and should be identified. But other infrared applications should not be overlooked when working in a power generation facility. These systems may include system equipment, electric generator components, and refractory-lined vessels. All of these play a critical role in the generation of power and are relied upon for safe and effective operation to keep the plant up and running
A few examples of problems found in such systems are presented below.
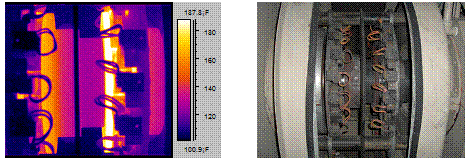
Figures 1a & 1b: An example of elevated heating on the right electro-ring on a field exciter
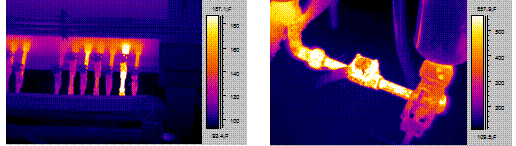
Figures 2a & 2b: Examples of steam blowing by a failed valve (2a) and a steam trap (2b).
Both of these problems were confirmed with ultrasound technology
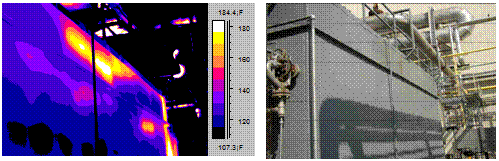
Figure 3a & 3b: An example of degraded refractory on the side of a co-generation unit
Substations
Substations are centralized places of electrical equipment where voltages are transformed up or down for transmission and distribution purposes. They are usually located outdoors within a fenced yard, but some are indoors. Substations are most frequently found at power generation plants, throughout municipalities and cities, and at large industrial and manufacturing sites.
The main piece of equipment in a substation is a transformer(s) that is used to transform electric voltages either up or down, depending on their design and service duty. Located on both the high and low voltage side of a transformer are breakers that serve as protection from electrical faults and switches that serve to join or isolate various circuits in the substation. Lightning arrestors are also found on the high and low side of transformers.
Depending on the type of transformer being used, a load tap changing (LTC) compartment, attached directly to the side of the transformer, may be present that is used to adjust voltages as load demands change. This is accomplished through a series of movable taps inside the compartment that occasionally fail and cause catastrophic damage to the transformer (figures 4a & 4b). If the transformer lacks an LTC compartment, then voltage regulators are present that perform the same duty. These are stand alone, oil-filled tanks located on the low voltage side of the transformer and closest to the outgoing circuit lines.
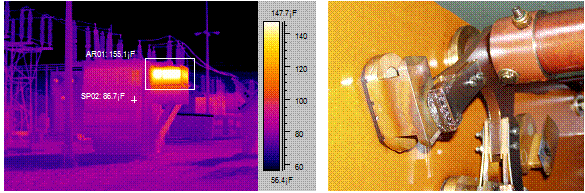
Figure 4a (left) shows a typical thermal pattern of a load tap changing compartment that has an internal problem. Figure 4b (right) shows the source of the heating on a movable contact that has been arcing.
Another not-so-common transformer problem that I have encountered involves the exterior cooling fins that promote proper oil circulation inside the tank. Normally, a warm to cool thermal pattern should be seen from top to bottom on the fins. Cold fins from top to bottom indicate either low tank oil levels or blocked fins that retard circulation (figure 5).
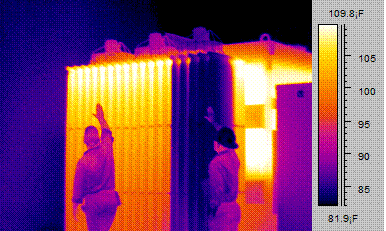
Figure 5: Shows a thermal pattern of cold circulation on the fins on the right side of this transformer.
Breakers also play an important role at a substation. Two main types occur outdoors in the substation yard, oil-filled and SF6 gas filled. While bolted connection problems between bushing and conductors are most common, internal bushing problems are most interesting to locate. Internal connections on the top side and the bottom side, which are usually hidden deep inside the tank, have been documented (figures 6a & 6b).
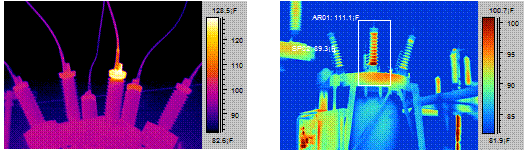
Figure 6a shows a heating pattern on the top side of SF6 breaker bushing and end cap.
Figure 6b shows a heating pattern on an oil-filled breaker bushing with a bottom side connection problem internal to the tank.
Lightning arrestors play an important role by dissipating harmful current surges due to lightning strikes. Arrestors are located on the high-voltage line entrance side of the substation and on the low-voltage circuit feeder side. One of our clients has witnessed station arrestors fail to complete destruction and consequently bring down a substation (figure 7). Any arrestor inside a substation that shows a temperature rise should be documented and flagged for replacement as soon as scheduling permits.
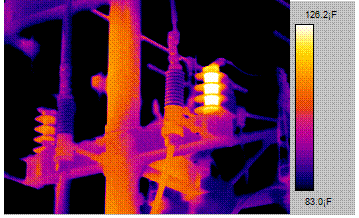
Figure 7: A warm arrestor that protects a 13kV feeder circuit exiting the substation.
This arrestor failed and brought down a substation feeding a citrus juice plant.
While most of the infrared inspections I have performed at substations have been conducted during daylight hours, scanning at night reveals new types of problems. Corona and tracking conditions are excellent examples. In most cases the delta-temperature observed when viewing these problems is small. The heating patterns can occur as ring shaped designs on insulators (figure 8a) and potheads and can also show up as hot spots between the bells on insulators (figure 8b).
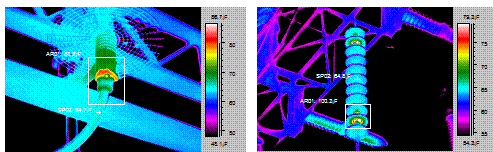
Figure 8a (left) shows corona on a 13kV pothead
Figure 8b (right) shows tracking on the skirts of a bell insulator
Transmission and Distribution
A majority of the transmission and distribution (T&D) work I have been involved with has been infrared inspection of overhead power lines and associated equipment. Although not covered in this presentation, thermal scanning of pad mounted switchgear, transformer vaults, and underground enclosures also constitute T&D infrared inspection work.
Transmission lines are easily identified by the large tower structures and massive spans of lines observed along major highways and throughout the countryside. These lines commonly transmit voltages at or above 69kV over long distances and they make up the main spine of a “power grid”. These lines generally start at power generation plants and supply power to transmission substations and switchyards and ultimately to distribution substations.
Some of the most common connections that occur on these lines are dead-end sleeves and splice sleeve connectors. These are compression fitted connections that join conductor ends to each other and to dead-end bell structures. The end-end sleeves occur at high tower structures and serve to join large spans of conductor lines to each other via a jumper wire. The splice sleeve connectors serve to join conductor ends to each other. These are commonly used to mend damaged or severed lines.
Standard delta-temperature infrared surveys are widely used by power companies to look for hot connections. Because of the vast distribution of these lines, they are accessed by land-based vehicles as well as aircraft and boats.
One particular job we were asked to perform a few years ago involved obtaining absolute temperatures on conductors, dead-end sleeves, and splice sleeves on a 230kV transmission circuit. The power company had concerns of increasing line sag and potential connection failures due to ever increasing load conditions brought on by new growth in the service area. Absolute temperature readings were necessary to compare the manufacturer’s thermal tolerances on conductor lines at given loads and between conductors and the sleeve connections.
To accomplish this project, a dead-end connection with a tag end of conductor cable that was recently removed from the field was used to calculate an emissivity of our target (figure 9a). The target was circular in shape with a diameter of roughly 2-inches. The ambient outdoor temperature was used as a background temperature for each connection location we examined. A set-back distance of 9 to 10 feet was calculated so that a 1/4-inch spot size would be achieved to capture our temperature readings from the sides of our circular targets (figure 9b). Naturally, bucket trucks had to be used to access our inspection points. For those of you who have never been in a bucket truck navigating though 230kV energized power lines at 50 to 80 feet above the ground, I can attest that it rivals any amusement park ride out there.
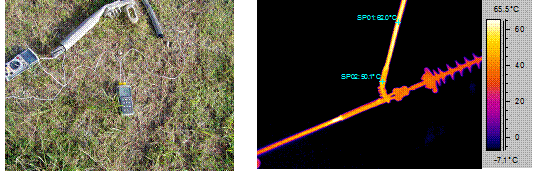
Figure 9a (left) shows a dead-end connector with two independent thermal couples measuring target surface temperature that was used to determine the emissivity of the connection’s surface
Figure 9b (right) shows a thermogram of a dead-end connector and conductor
The distribution side of the T&D sector includes overhead and underground equipment that is responsible for the delivery of power to the commercial, industrial, and residential communities. These distribution circuits, called “feeders”, originate from substations. It is common to have several feeders from one substation service a given area and have the feeders “tie” with one another via switches that occur along various points on the lines. These switches are used to back-feed and to isolate portions of feeders during repairs and temporary power outages.
Delta-temperature infrared inspection is the most widely performed inspection on this equipment. Fluctuating seasonal and daily loads combined with environmental and end-user wear and tear requires continual maintenance and repair of this equipment. I have several clients that contract infrared services on an annual basis, and it is no surprise that every year we find new problems in their system.
While generic infrared scanning of feeders is most common, specially tailored inspection programs can be beneficial to monitor installation practices and to troubleshoot problems on critical pieces of feeder equipment. An example of such a program was a couple of years ago when my company performed a thermal and visual inspection of non-fused 13kV and 23kV feeder switches. Over 6,000 switches were inspected during this eight month long project. Baseline thermal images were documented for each switch as were thermal and visual exceptions. The results of this inspection provided valuable insight on installation practices, the reliability of lightning arrestors being used and headed-off numerous failures that would have brought down feeder circuits. Figures 10a, 10b, and 10c provide examples of common problems found during this investigation.

Figure 10a (left) shows a failed lightning arrestor
Figure 10b (center) shows heating on a bolted connection and jumper wire
Figure 10c (right) shows heating on a switch receiver / jaw contact
Another specialized project we performed for a large utility company involved the infrared inspection of nearly two hundred 13kV and 25kV get-a-way poles. A get-a-way pole is the first switch pole of a feeder circuit as it exits a substation. In many cases, the circuit travels underground for up to two miles from a substation before it makes an appearance to start an overhead feeder (figure 11a) . The results of our inspections revealed a repeated pattern of heating on two-hole pad conductor connections to vertically mounted switch frames (figure 11b). Initially, it was thought that torque specifications on these connections were not followed, but this was ruled out when newly installed connections using specified connection torques were showing up hot. The utility eventually contacted the manufacturer and found that the beveled holes on the switch frames were not being milled deep enough to allow the proper seating of the washer and bolt, even when the proper torque requirements were being met.
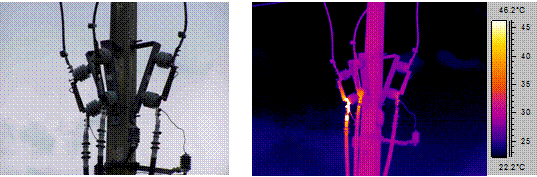
Figure 11a (left) shows a typical Get-A-Way pole consisting of vertically mounted switches, potheads that terminate the conductors and lightning arrestors.
Figure 11b (right) shows an example of a repeated heating pattern discovered at the pad connection between the conductor pothead and the switch frame.
Finally, there are those not-so-common problems that a thermographer stumbles upon every so often. For me it was this past summer during a delta-temperature scan on a 13kV feeder. I happened to see an eye-bolt supporting a neutral line on a lateral feed in a neighborhood that had a temperature rise of over 65 F degrees (figures 12a and 12b).
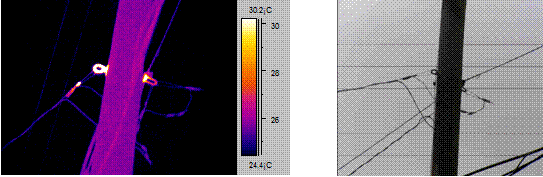
Figures 12a and 12b show a hot eye-bolt on a power pole that supports a neutral line.
It was discovered that the bolt was hot because of an open neutral that was causing the return current on the circuit to be rerouted from the neutral pathway to a grounded object; in this case the eye-bolt.
Common problems experienced with an open neutral are lights that burn dimmer on some circuits and others that burn brighter on other circuits. Also common are lights that flicker or turn brighter when heavy loads are applied, such as an air conditioning unit turning on.
Having an open neutral is a dangerous situation that should be corrected as soon as possible. The ground is now energized and can cause injury to someone coming in contact with any bare metal that is intended to be grounded. Not only did the discovery of this problem save unknown amounts of time to locate, it also prevented possible serious injury to an unsuspecting utility worker.
Conclusions
There are numerous applications for infrared technology in the electrical utility industry. Power plants, substations, and transmission and distribution equipment present unique opportunities for the curious thermographer.
Sometimes the discovery of not-so-common problems can have huge dividends like preventing outages, or in some cases injuries to utility workers.
Specialized infrared inspection work also has its place in the utility industry. Evaluating operating conditions to predict future capacity capabilities as well as installation and manufacturing specifications are all within the realm of infrared applications.
Visit out Sponsors:
Electrophysics
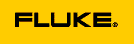

