Marie Getsug
Senior Consultant, M&R Services
Commissioning Agents, Inc.
Clarksville, MD 21029
www.cagents.com
Abstract
Identifying Original Equipment Manufacturers (OEMs) with the capabilities, expertise and experience to design, build and deliver physical assets that perform beyond the stakeholders’ expectations is an important initial step in delivering a successful project. Identifying all the stakeholders and their interests is critical to accomplishing this objective. Not identifying all the stakeholders may be the biggest mistake project managers make across the board to jeopardize the long-term performance & Life Cycle Costs (LCC) of the assets their capital projects introduce. By limiting the stakeholders identified at the “Initiate” phase of a project, the User Requirement Specification (URS) and supporting engineering specifications and standards lack the depth to represent all the “Users” and objectives for the project. When tunnel vision sets in at this early phase of concept and design, focusing in on the traditional cost, scope and schedule to define a project, the opportunity to raise the bar on the LCC and long-term performance is often lost before it’s even defined.
This white paper will explore the following topics core to engaging OEMs interested and capable of influencing reliability and automation in their designs by integrating all the stakeholders’ requirements:
- Stakeholder Identification and Analysis
- Request For Information (RFI)
- Project Management Phases & Front End Planning
- Project Management Phase Gate Criteria
- Request For Proposal (RFP)
- Design For Reliability (DfR)
- Automation & Process Analytical Technology (PAT)
- Life Cycle Cost & Maintenance Strategy Development
- Training & Documentation Requirements
- Commissioning & Performance Criteria
- Criteria To Break A “Maintenance Standard” Threshold
- Criteria To Introduce A New Technology
Discussion
As depicted in the following Figure, the level of influence is greatest at the earliest phases of the project and this is why it is so critical to ensure all the interests, functional requirements, and user requirements have been gathered from all those affected throughout the life of the asset.
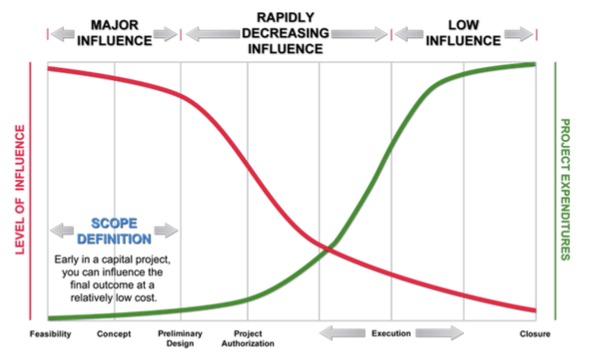
Stakeholder Identification and Analysis
Identifying the stakeholders goes far beyond including the internal departments represented within the buyer’s organization. OEMs, contractors, vendors, and other outside suppliers represent a group of external stakeholders often not invited to participate in the project at all. What opportunities are missed as a result of this oversight? The opportunity to engage this group of professionals and experts to apply
their expertise to a project and to gain their ownership to achieve not only the objectives of all the other stakeholders identified, yet to exceed their own expectations. A tool carefully constructed to identify the OEMs, contractors, vendors, and suppliers who can partner at this level is the RFI. This RFI tool should be used to inquire about the capabilities, expertise, and experience a company has to qualify them as worthy of receiving an RFP.
A thorough stakeholder analysis not only defines the stakeholders, their interests, attitudes and concerns, yet also goes beyond the typical problem resolution. It should go beyond current problems and seek opportunities to deliver more by leveraging and integrating both the requirements and expertise of the project team. The more the project team can be engaged and have ownership of the project up front, the more likely they will be to contribute their expertise and innovations.
“Wrong decisions made early can be salvaged, but ‘right’ decisions made late cannot.” Jerry Madden, NASA PM
Request for Information
An RFI is an inquiry into the standard practices of a company so as to quantify and qualify their capabilities, desire, expertise and experience to take a project from concept to operation and deliver the value and performance the project requires. The questions should be open ended without leading, in order to allow each company who responds to demonstrate what they typically bring to a project and partnership. The RFI is a tool used to determine who is invited to respond to the RFP and should weed out those companies unable to meet the projects’ and stakeholders’ expectations or perform as a partner.
Recognizing that the biggest opportunity lies in being involved in the design and selection of the system/equipment, identifying those OEMs who are most willing and capable of participating and contributing at this early phase, provides a strategic advantage and value to the overall project.
1. As much as 60% of failures & safety issues can be prevented by making changes in design1
2. 80% or more of a facility’s life cycle cost is fixed during the plan, design & build phases2
3. 30-40% of equipment breakdowns are related to poor equipment design or condition3
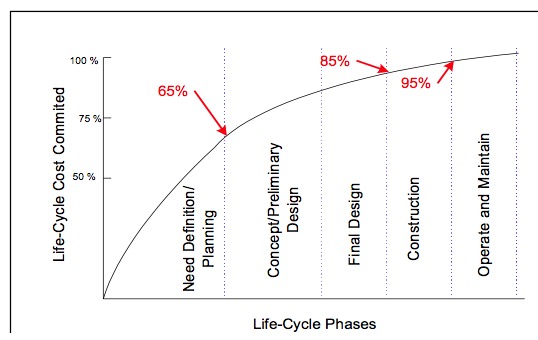
Identifying OEMs, suppliers, vendors and contractors with expertise in the maintenance and reliability profession who can translate their expertise into the equipment, options, documentation, training, and services they supply is paramount to achieving the goal of each capital project. Requesting a company’s ability to support requirements with respect to an asset’s lifecycle should be considered while developing the content of the RFI.
1 Ramesh Gulati: Maintenance and Reliability Best Practices, second edition – page 181
2 Dr. Benjamin S. Blanchard: Design and manage to life cycle cost, 1978, PB – M/A Press
3 Ron Moore: Making Common Sense Common Practice, fourth edition – Chapter 2
The following sample of categories provides a foundation for preparing such a document:
Request for Information – Categories
- Requesting Company & Project Overview
- Convey the Company’s vision and mission
- Provide the charter information for the project
- Responding OEM, Contractor, Vendor, Supplier profile
- Company culture and core values
- Leadership and Subject Matter Expert (SME) resumes
- M&R / Asset Management experience & certifications
- Detailed list of Services provided in various markets
- References & Previous engagements with Buyer
- Safety, Protective Devices, Alarms, and Interlocks
- Machine Specifications
- Life Cycle Costing (LCC)
- Environmental Conditions
- Instrumentation & Automation
- Baseline Performance and Precision Techniques
- Settings vs. Adjustments
- Maintainability, Serviceability, Operability, Accessibility & Clean-ability
- Service Contracts
- Maintenance Strategy Development
- Reliability Centered Maintenance (RCM) Methodology
- Design for Reliability (DfR)
- Equipment Design Improvements and Process
- Performance Criteria, Warranty, and Guarantee
- FAT and SAT Protocol and Criteria for Performance & Payment
- Performance Measures
- Documentation (eTOP, O&M Manual, CMMS, training, BOMs etc.)
- Spare Parts and Components (CMMS format)
- Training for Operators, Maintenance, Automation, and Metrology, etc.
- Workflow Diagrams
- Specifications, Standards, and Guidelines
The RFI is the opportunity for the responding company to highlight their capabilities and willingness to partner and participate in the project. Look for responses and examples in each of these categories that demonstrate the company has already done this, if not for their clients, certainly for themselves. Give the respondents the opportunity to differentiate themselves from their competitors. Consider closing the RFI with the following questions:
- What projects have you delivered and industry contributions have you made that clearly demonstrate your cutting edge leadership in delivering an asset, system, project or process that is designed to achieve all aspects and interests depicted in this RFI? Provide details and examples
- What expertise do you have with integrating predictive maintenance technologies into your designs?
- How does your company integrate the expertise of each of the functions supporting the concept, design, build, and on-going performance of the solution you are proposing? How does your company represent these functions and capabilities in a unified approach as a stakeholder and partner with your client for a project such as this one? Provide details and examples
- What options do you offer for the solutions you provide and what options are you currently developing? What driving factors are there behind these options and offerings (why have you developed these options)? What new failure modes might these new options introduce and what mitigation strategies are you applying to address these new failure modes?
- What hasn’t been asked that you would like to share to highlight your expertise and ability to partner on this project in order to provide the best life cycle solution possible?
Ensuring a strong collaboration and clear expectations and criteria are in place among procurement, engineering, quality, production, automation, and maintenance & reliability within the buyers company before the RFI is sent out is critical to ensuring that only those who achieve the agreed upon RFI threshold will be invited to respond to the RFP. A formal review, such as a decision diagram style matrix, of the returned RFIs should be performed to rate the responses as well as the importance of each of the criteria and develop a quantitative score for each response. A minimum score should be agreed upon as a threshold for moving an OEM, supplier, vendor, and/or contractor to the RFP phase.
Many OEMs, suppliers, vendors, and contractors will not respond to an RFI. It may be necessary to spend time describing why their response is so important if they want to be considered for the RFP.
Ultimately, the RFI is often the missing tool at the concept / initiate phase of a project that should eliminate those who are not prepared or capable of meeting the expectations of the requesting company and the given project. Without this, RFPs are often sent to unqualified OEMs, suppliers, vendors, and contractors resulting in the initial investment becoming an impediment to considering the life cycle cost (LCC) and performance. Further, there is typically an already agreed upon dollar value in the capital plan for a particular project, thus adding financial pressure to make a short-term vs. long-term decision. This approach can hinder the buyer from obtaining the expertise and the options that support the more reliable and user-friendly solution designed for the life of the project. Bring out the best in your OEMs, suppliers, vendors, and contractors by giving them the opportunity to reply to an RFI.
Project Management Phases & Front End Planning
Before moving on to the RFP phase, let’s explore a critical process that needs to be in place, in the buyer’s organization, to ensure the best solutions that are presented by OEMs, suppliers, vendors and contractors, as well as other stakeholders are identified and considered. The traditional five phases of a capital project include initiate, plan, execute, control, and close as depicted in the Figure that follows.

Incorporating a structured front end planning process into the project life cycle processes provides the structure to ensure these tools are applied. Front end planning is defined as “the process of developing sufficient strategic information for owners to address risk and decide to commit resources to maximize the chance of a successful project”. This process encompasses three sub-phases: feasibility, concept, and detailed scope. In many organizations, each of these phases is checked at “phase gates” that must be passed or approved prior to moving to the next phase. The following Figure depicts the front end planning sub-phases per the Construction Industry Institute (CII).
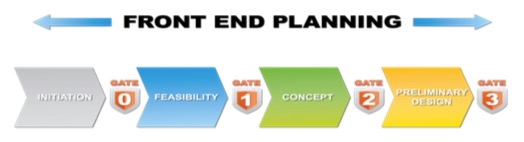
Front end planning generally ends at phase gate three (after detailed scope) with project approval to move into detailed design and construction, unless the project is terminated at this or an earlier gate. The front end planning sub-phases are preliminary to the execution and project closure phases as depicted in the following Figure:

Project Management Phase Gate Criteria
The preparation required of a disciplined phase gate approval process ensures that the criteria are met prior to securing approval to advance to the next phase of the project. Thus, the importance of having the criteria for ensuring the most competent and capable OEMs, supplier, vendors, and contractors identified and agreed upon is core to ensuring the value they can offer is realized. Typical phase gate criteria in the front end planning process include the following examples:
- Gate 0: RFI
- Gate 1: RFP/URS – including M&R & Automation Specifications and Standards
- Gate 2: Alternatives Analysis, LCC & Options/DfR – Design for Reliability
- Gate 3: OEM Performance Criteria/Documentation Requirements/Maintenance Strategy Requirements/Training Requirements
The Construction Industry Institute (CII) performed a study focused on collecting data to support the use of a structured front end planning process on capital projects. Alignment, also one of the four foundational elements of the new ISO 55000 Asset Management Standard, was recognized as an important factor during successful front end planning and is considered a CII best practice. Alignment is defined as “the condition where appropriate project participants are working within acceptable tolerances to develop and meet a uniformly defined and understood set of project objectives”. Data was collected in the CII study, RR213-11 – Data Analysis in Support of Front End Planning Implementation4, to investigate alignment’s effect on the front end planning process and overall project success. A total of over 600 projects were used in this analysis representing almost $37 billion in total installed cost. The industry average results of “good” front end planning efforts included:
- Costs: 10% lower overruns
- Schedule: 7% shorter delivery
- Changes: 5% fewer
Front end planning is typically considered complete when the basic engineering and design is complete and the project is ready to start detailed design. The following are finalized in front end planning:
- Site selection is finalized
- Business objectives are clearly defined
- Technologies are selected
- Project alternative(s) have been evaluated and selected, including flexible design strategies
- Scope is defined and baselined
- Risks are identified, quantified and/or qualified; mitigated
- Resources and staffing are selected; roles clearly defined
- Costs and schedule are finalized and aligned with scope of work
- Project execution plan is complete
- Project team and stakeholders are aligned
- Ready to start detailed design
4 Construction Industry Institute – RR213-11 – Data Analysis in Support of Front End Planning Implementation https://www.construction-institute.org/scriptcontent/more/rr213_11_more.cfm
Having this structure in place is what ensures the maintenance, reliability, automation and other excellence tools get applied while the opportunity to influence the life cycle cost and performance is still possible. Missing the application of these tools during this phase of the project may be one of the biggest lost opportunities in capital projects.
Request for Proposal
The most important document to prepare after the RFI is the RFP and all the supporting documents it comprises, including the URS. The URS typically establishes the known requirements of the project; however, it often neglects to include the interests, specifications, and standards of many of the stakeholders and functional departments that will operate, control, maintain, analyze, and monitor the project over its entire life cycle.
Several recommendations including who to involve, how to capture this information. and what to request from the OEM, supplier, or vendor include:
- An approach based on an asset management program with a policy that supports the commitment to have a cross-functional team participate in the capital project process
- A team of operators, technicians, and other key stakeholders who will be responsible for operating and maintaining the assets to contribute their recommendations and requirements as input through the design phase, starting with the URS
- Leverage known concerns and limitations of current similar systems by collecting the supporting data and experience such as the following:
- Interview operators and technicians to capture this experience can be an effective way to document historical experience on like equipment
- Analyze the CMMS data for like equipment to identify the repeat failure modes, spare parts concerns and usage among other performance information in an effort to ensure historical concerns are addressed with the new project and design is time well spent
- Detail the maintenance, reliability, instrumentation, automation, production, sanitation, training, procurement, precision, quality, and other specifications and standards represented in the facility or facilities that the project will reside is paramount to leveraging the existing systems
- This document establishes the criteria to address the maintainability, operability, sample-ability, clean-ability, accessibility, rig-ability, precision, and reliability requirements desired
Recommendations regarding what to include in the URS, engineering specifications and standards, or as supporting standalone documents include the following:
- Engineering specifications should include the standards adopted by the production, maintenance, quality, and reliability teams to remain consistent with the common spare parts, training, work plans, and theory of operation currently in place
- Engineering standards should include details that support the company’s on- condition monitoring, predictive technologies, evidence based maintenance, automation and instrumentation requirements to trend and monitor for abnormal conditions
- Autonomous maintenance requirements for operator involvement with an emphasis on settings vs. adjustments for any tooling that changes with sizes or products
- Precision specifications detailing required tolerances, torque, alignment, and balancing standards for technicians
- An asset database for commissioning and validation activities, leveraged with procurement and maintenance and reliability requirements, to minimize repeat data and incorporate information from OEMs, contractors, integrators, and consultants
- A maintenance mitigation strategy that is technically feasible and worth doing – initially requested from the OEM, supplier, and/or vendor
- OEM experience based maintenance strategy to reduce frequency based maintenance and apply on-condition, evidence based, predictive tools and techniques to monitor and trend performance non-intrusively
- Preventive and corrective work plans and required parts, tools, and instructions to address failures when they occur, including identifying and, in some cases, stocking parts so they are readily available to preserve the function the asset provides
Design for Reliability (DfR)
During conceptual design, analytic tools such as DfR can be used to anticipate the expected failure modes and effects associated with different design configurations. The resulting information allows for a final design that promises the best performance of output, reliability, and life cycle operating cost. DfR is applied with the goal of designing out failure modes rather than mitigating them. This allows the expertise of maintenance, reliability, production, quality, and engineering team members to apply their experience and standards with specific manufacturers, OEMs, and data driven preferences in drive systems, lubrication, on-condition monitoring, instrumentation, automation, reliability specifications, standards, precision specification, and other factors to influence the design of the asset.
In addition, the following DfR attributes should be incorporated in the layout and design:
- Maintainability – ability to access and maintain the components of the asset for maintenance and monitoring
- Reliability – ability for the asset to run reliably
- Rig-ability – ability to rig the asset and its components (motors, agitator shafts, gear boxes, etc.) in and out after the initial installation, including tie off points designed for the equipment and the technicians accessing and maintaining it
- Clean-ability – the ability to clean all areas of the equipment and maintain the classification of the area in which it resides, including inside the equipment
- Accessibility – ability to access the components of the asset for the purpose of production, sanitization, sampling, maintaining, monitoring, etc.
- Operability – ability to operate the asset with ergonomic layout considerations and minimized value mapping requirements
- Visual Factory – application of 5S and Total Productive Maintenance (TPM) autonomous maintenance concepts such as marked gauges, standards in colors, schemes, automation, physical layouts, etc.
Many times the above criteria are accomplished using a checklist of review items for each phase gate to ensure all the standards and concerns are captured and addressed for each new asset and system.
Automation & Process Analytical Technology (PAT)
PAT is considered to be a system for designing, analyzing, and controlling manufacturing through timely measurements (i.e., during processing) of critical quality and performance attributes of raw and in-process materials and processes with the goal of ensuring final product quality. It involves defining the Critical Process Parameters (CPPs) of the equipment used to make the product, which affect the Critical Quality Attributes (CQAs) of the product and then controlling these CPPs within defined limits. This allows manufacturers to produce products with consistent quality and also helps to reduce waste & overall costs.
PAT is applied to leverage the automation for the asset by identifying and trending pending quality and reliability failures with instrumentation triggers. Typically, PAT is only used to monitor “Critical Control Points” (CCPs) that define the Validated State of the system. By taking a more comprehensive approach to asset management, these same CCP’s can be monitored to indicate asset health. Since many of the Quality Parameters are instrumented, it is beneficial to leverage these instruments by trending the information, rather than just establishing a threshold for quality to monitor whether each cycle is within compliance or the validated state.
Life Cycle Cost & Maintenance Strategy Development
After the initial results of the RFP are secured, the following initiatives to determine the life cycle cost options and develop an appropriate maintenance strategy for the projects’ assets should be determined as the design is finalized and optimized:
- Life cycle cost analysis should be performed and used as the basis for procurement activities to encourage the inclusion of reliable design features and discourage procuring assets based solely on their initial cost
- A risk based impact / asset criticality assessment should be performed to identify the most critical assets from a product quality and reliability perspective, accomplished by the cross-functional project team
- A maintenance strategy should be developed, based on the results of the asset criticality and impact assessment, via a defined methodology such as RCM for the new assets by incorporating the team’s insights on the operating context and sequence of operations, and shared perspectives on the failure modes
- The maintenance mitigation strategies must be technically feasible and worth doing
- Preventive, predictive, and corrective work plans and required parts, tools, and instructions to address failures when they occur, including identifying and, in some cases, stocking parts so they are readily available to preserve the function the asset provides
Training & Documentation Requirements
Providing the project teams with an overview and training regarding the benefits of applying FEP and how to apply these tools with the OEMs, suppliers, vendors, and contractors is core to the success of the project.
A presentation can be used to provide an overview of maintenance and reliability concepts for project managers, engineers, and manufacturing leadership. The following Figure depicts the aspects core to this training. It is recommended that the course objectives include the following:
- Value provided by applying FEP and Maintenance Excellence (MEx) concepts including the OEMs, suppliers, vendors, and contractors as stakeholders in the initial phase of the project
- Introduction to the importance and application of reliability centered design and its impact on lifecycle costs
- Introduction of basic M&R terms and definitions
- Discussion of critical aspects that should be considered in any new project
- Introduction of the six failure patterns and the Potential-to-Functional (P-F) failure curve and how to apply these to the development of design and assets and their maintenance strategies
- Identification of what asset information is required to conduct an RCM analysis (what to request from vendors/OEMs)
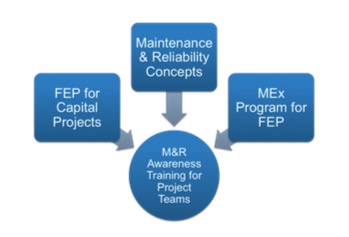
Ensuring the required documentation and training are available in the required format is a frequently overlooked activity. Leveraging the automation already required on a new asset or system can provide a platform for both the documentation as well as training via both work instructions as well as videos. Requesting this intellectual property early in the design and concept phase can identify those providers who have already established this level of integration. In addition to the documentation, ensuring an expert trainer is provided to teach the content to the operators, technicians, integrators, and engineers is also invaluable. Often a qualification test in both a written and practical format can ensure the training is effective. This should be specified. Specifying the results of the training is often underestimated and can lead to a lack of ownership by those operating and maintaining the equipment.
Improvements made by the OEM, supplier, vendor, or contractor after an asset has been purchased, installed, and commissioned often address repetitive failures others have experienced and as such should be written into the contract as documentation that will be provided in the future. Language such as the following can be included in the documentation as well as contractual / warranty requirements:
- Buyer must be advised for the life of the asset when a publicly available modification is available to the design of equipment or systems installed within 2 weeks of the available modification
- This includes the following examples:
- Changes to design out the failure modes of repeat failures in next generation equipment
- Any system modifications or redesigns
- Providing all supporting documentation for the revised designs and solutions
- Identifying potential failure modes the new design may introduce and the recommended mitigation strategies
Commissioning & Performance Criteria
The final stage prior to turnover is commissioning, verification, and validation. A poorly installed project is just as likely as a poorly designed project to create long-term operating problems and increase life cycle costs. After vetting the asset and system design to optimize performance and reliability, it needs to be installed and tested to ensure it is operating to specification. Up to 70% of failures occur during the start-up phase (‘infant mortality’), almost always due to design, installation, and/or procedural errors.
The following contractual and performance acceptance testing language is provided for consideration in options and examples of how to hold the OEM or supplier accountable legally and contractually via the agreements in place for the project requirements and expectations. The more proactively these are applied, starting with establishing the expectations at the RFI phase, the more likely the OEM and/or supplier will be prepared to deliver these expectations and the supporting results.
- Performance Guarantee
- A performance guarantee is a promise made that the equipment lives up to certain calculated performance criteria and expectations, or that a product will continue to perform well over a stated time period
- The goal is to define the company’s commitment and extent of future responsibility
- A performance guarantee in the form of a written legal contract should be written to meet a defined technical efficiency
- Vertical Start-up
- The term vertical startup refers to meeting all objectives for any project or initiative on day one. In essence, ”doing it right the first time”
- Including a vertical startup clause in the performance guarantee and payment terms demonstrates the importance and value of manufacturing product immediately and to specification
- A vertical start-up guarantee in the form of a written legal contract should be written to meet a defined technical start-up “exponential curve” and schedule
- Warranty
- The Warranty Period applicable to this system is a given time period measured from the date the equipment is capable of making sellable product at the final performance levels
- Warranty can include parts, labor, travel, and expenses for all equipment
- Service Contracts
- Buyer must be able to secure service response times (within first year of service from start-up of equipment) as depicted below:
- Parts delivery response with regards to meeting established lead times
- On-line/phone technical support 24-7
- On site service support response within 24 hours
- Inquiry response time to a non-emergency inquiry within 24 hours
- Buyer must be able to secure service response times (within first year of service from start-up of equipment) as depicted below:
- Equipment Design Improvement Notification
- Ensuring design improvements made after the equipment is delivered are communicated back to the buyer in a timely fashion is the intent behind this notification
- Equipment design improvement notifications are also described in the documentation section
- Factory Acceptance Testing (FAT) – at the vendor’s facility by individual piece of equipment
- The FAT is a combination of verifying individual machine design elements and re-start capabilities
- The FAT will be performed through a sequential series of defined protocol for the following aspects for each machine / asset purchased:
- Static Inspections
- Dynamic Pre-testing
- Induced Failure Testing (IFT) – the ability to restart from a failed condition
- Site Acceptance Testing (SAT) – by individual piece of equipment at the Purchaser’s site
- The site acceptance testing shall be scheduled by the Purchaser within the first few weeks after the start of sellable production
- Vendor shall facilitate the repair, replacement, or adjustment any component of vendor’s equipment failing this portion of the test, (unless vendor’s technical representative can demonstrate that failure was a result of improper installation) and re-conduct the test until the equipment is successful in passing
- If vendor’s technical representative identifies errors or omissions in the installation practices, or if component failure is shown to be the result of improper and/or non-obvious installation error the purchaser will direct the installer to make corrections at installer’s expense
- The purchaser will provide reasonable quantities of product, packaging materials, and operating personnel to conduct this test
- The vendor’s representative will assist the purchaser in conducting test runs of the equipment and can assist in the operation of the equipment to meet the performance targets outlined
- The minimum requirements by the purchaser to conditionally accept the system should be defined in detail
- End-to-End Acceptance Testing – operated once installed at the purchaser’s site
- The purchaser shall schedule the end-to-end acceptance testing within a few weeks after the successful completion of the site acceptance
- If vendor’s equipment cannot successfully pass the end-to-end acceptance testing, then the vendor shall repair, replace or adjust any component, which is the cause of such failure, at vendor’s expense
- If failure to pass the test cannot be traced to a failed component, but is more likely the result of a deficiency in design or construction of the equipment, then the vendor shall (at vendor’s expense) modify (or replace) the equipment (subject to the purchaser’s approval) in order to bring the equipment into conformance
- If vendor can demonstrate that non-performance is the result of other factors on the line, outside the control of the vendor’s equipment, the purchaser will direct a decision to either correct the offending factor or to accept vendor’s equipment as installed
- The purchaser will provide reasonable quantities of product, packaging materials, and operating personnel to conduct this test
- The minimum requirements by the purchaser to conditionally accept the system should be defined in detail
- Operating Equipment Effectiveness (OEE) – Performance Criteria
- The system will be required to meet defined OEE
- OEE quantifies how well a manufacturing unit performs relative to its designed capacity, during the periods when it is scheduled to run
- OEE breaks the performance of a manufacturing unit into three separate but measurable components: availability, performance, and quality
- Each component points to an aspect of the process that can be targeted for improvement
- OEE may be applied to any individual work center, or rolled up to department or plant levels
- This tool also allows for drilling down for very specific analysis, such as a particular part number, shift, or any of several other parameters
- It is unlikely that any manufacturing process can run at 100% OEE
- Many manufacturers benchmark their industry to set a challenging target; 85% is not uncommon
- The minimum OEE requirements by the Purchaser to conditionally accept the system should be defined in detail
- Technical Efficiency Calculations and Requirements
- The system will be required to meet a defined technical efficiency
- Product not in sellable condition, either not caused by vendor’s equipment, or product which is outside acceptable quality target limits set for the vendor’s equipment shall be converted to an equivalent-time basis and subtracted from the operational time
- Downtimes resulting from material defects, unavailability of product, operator-error, or caused by other equipment on the line, will be subtracted from the total test time
- Performance Based Payment Terms
- The payment terms should be defined and provided for clarity on how to hold the OEM or supplier accountable legally and contractually via the agreements in place for the project requirements and expectations
- Early Failure Expectations and Requirements
- Ensuring early failure is clearly communicated as unacceptable, the following language supports holding the OEM, supplier, vendor, and/or contractor responsible for this
- Examples of this include requesting the following information and commitments:
- Providing a list of all the consumable parts and spare parts and the guaranteed minimum Mean Time Between Failure (MTBF) for each
- Committing to immediately address any spare or consumable part with a MTBF of less than 6 months with an acceptable alternative providing a MTBF guarantee of greater than 6 months
- Any spare part or consumable part requiring operator or technician attention more than monthly creates quality or reliability concerns that must be identified and have alternatives presented for longevity
- Early failure of assets, components, consumables or spare parts will be factored into the machine’s technical efficiency and performance
These performance criteria should provide recommendations and guidance on holding the OEMs, suppliers, vendors, and contractors accountable to performance criteria in support of the project and for the life cycle of the asset. This performance criteria and contractual language can be referenced or used in the MSA (Master Service Agreement), RFP (Request for Proposal), P.O. (Purchase Order), performance guarantee and other supporting contracts as well as the FAT, SAT, and end-to-end acceptance testing protocols among other documents to achieve the objectives of the project.
Criteria to Break a “Maintenance Standard” Threshold
Formalized maintenance standards are becoming more and more common, where methods, tools, and equipment are selected that fit into a larger asset management strategy. As an example, a particular site may opt to apply a G1.0 balancing standard for specific fans and a given brand for PLCs. The value of maintaining such criteria on a capital project under normal circumstances is clear to any M&R team; however, project engineers typically like to identify the latest and greatest technical solution available. How does the project team handle such a situation? When is such a change of value? That is the nature of this question – at what point does the value of a new technology or solution become significant enough to break the current “maintenance threshold”? By exploring the value and opportunity brought about by some new technologies and the application of a quantitative and qualitative LCC analysis, the variables and risks can be weighed and planned for while deciding whether the new solution demonstrates enough value to make it worthwhile to break the maintenance and/or reliability standard and pursue it as a solution. Certainly, the additional challenge of working with sole suppliers for a new technology or one that holds a patent or builds the equipment that delivers the required solution can also be explored with recommendations on how to leverage the risks and benefits in such a situation.
It is recommended to evaluate and document the common interests and those related just to M&R or project engineering at the concept phase of the capital project process to address these concerns by ensuring collaboration and consideration with the initial “numbers” early in the concept phase of the project and before the budget is established.
The goal of including M&R as stakeholders in the capital project process is to share the interests and experience of the M&R professionals who take care of the capital project assets after they are installed so as to improve upon the overall long term success and reliability of the project and assets. With this shared goal in mind and by using LCC as the basis for making capital project decisions, better decisions and long-term investments will be made by the capital project teams and represented in the capital project and FEP Processes.
Two additional considerations impact the success and long-term viability of a capital project. These involve which, of several options, is chosen and will a new technology be introduced as a result of a capital project. Although both of these can have significant impact on the LCC of the project, they can also be considered using a more indirect or risk-based approach to categorizing the impact.
If a “maintenance standard” is to be broken or challenged, the benefits must be more than what is required with a typical ROI for an improvement. Breaking the “maintenance standards” and best practices typically adds not only complexity and risk yet also reduces the potential for success. When a standard is established by maintenance, it means the spare parts, training and experience with that standard are already embedded in the operators and technicians within a given facility. For a capital project to introduce new or different components, OEMs, suppliers, and vendors or suppliers typically means introducing and supporting an entirely new learning curve for the operators, technicians, engineers, and M&R Team. This applies to the training, troubleshooting, spare parts, and many other factors. As a result, the complexities and risks must be carefully analyzed and if possible, the facility where the change will be introduced should be educated and involved with the decision to change in the concept phase for it to have a strong chance for success.
Criteria to Introduce a New Technology
Establishing a threshold for new technologies is an area often not explored with the stakeholders who will be responsible for 90% of the life of the asset. This can be addressed with the following criteria:
- A written threshold should be established for engineering that demonstrates technical superiority, technical advancement, and reliability before deviations from the maintenance and reliability standards are considered for a new project
Similarly, introducing a new technology can be risky. As much as this will be evaluated on an indirect basis, there are additional considerations that warrant careful contemplation.
Considerations should include the following prior to introducing a new technology into a facility:
- Impact on the theory of operation
- Impact on the sequence of operation
- Consider whether the above will rival existing equipment that will remain
- Consider the skill level of the facility’s technicians and operators to operate and maintain
- Consider applying DfR to the new technology
- Consider options and asking other maintenance and reliability teams who have introduced this new technology what the biggest challenges and surprises were
- Ensure the OEM is open to improvements, DfR and the long-term success of the project
As a result, the complexities and risks must be carefully analyzed and if possible, the facility where the new technology will be introduced should be educated and involved with the decision to change in the concept phase for it to have a strong chance for success.
Conclusion
With the introduction of the ISO 55000 Asset Management Standards focusing on life- cycle cost and risk-based performance this is a seamless opportunity to integrate the OEMs, suppliers, vendors and contractors as stakeholders in the FEP of the capital project process. The foundational elements of the ISO 55000 Asset Management Standard are clearly applied with this process. These four foundational elements include:
- Value – assets exist to provide value to the organization
- Alignment – asset management translates the organizational objectives into technical and financial decisions, plans, and activities
- Leadership – leadership and workplace culture are determinants of realizing value
- Assurance – asset management gives assurance that assets will fulfill their required purpose
By applying these tools and techniques, with all the appropriate stakeholders, it is the authors experience and expectation that you will have a significant impact on the ultimate design, reliability, and success of your projects throughout the entire life cycle of the assets and systems they support. By giving your OEMs, suppliers, vendors, and contractors the opportunity to perform as a partner to contribute to a higher standard of optimizing the design, maintainability, reliability, and performance of the assets they build the project objectives can be greatly exceeded. This provides not only an innovative way of achieving the complete vision and charter of the team yet demonstrates the goal of an asset management program – just like quality and safety – asset management becomes everyone’s responsibility.
References
1 Ramesh Gulati: Maintenance and Reliability Best Practices, second edition – page 181
2 Dr. Benjamin S. Blanchard: Design and manage to life cycle cost, 1978, PB – M/A Press
3 Ron Moore: Making Common Sense Common Practice, fourth edition – Chapter 2
4 Construction Industry Institute – RR213-11 – Data Analysis in Support of Front End Planning Implementation; https://www.construction-institute.org/scriptcontent/more/rr213_11_more.cfm