Adrian Messer
Manager of US Operations
UE Systems, Inc.
Ph: 864-224-4517 Cell: 914-282-3504www.uesystems.comAbstract
Airborne and structure-borne ultrasound technology has become a major player in predictive and preventive maintenance. Ultrasound has been proven and accepted by maintenance and reliability professionals globally across many industry and manufacturing sectors. With the advancements in technology and software, potential electrical and mechanical failures can be diagnosed early; therefore, allowing for more time to plan, schedule, kit, and perform work that would have otherwise been more reactive. Using ultrasound for condition monitoring impacts costs, increases productivity and best of all, improves safety. This presentation will focus on remote continuous monitoring applications using ultrasound, the need to monitor assets continuously for improved asset health measurements and data, and where we are seeing more and more guarding and shielding of assets. Remote monitoring with ultrasound can become a critical tool to help you continue to safely monitor your assets.
Introduction
Airborne and structure-borne ultrasound is a technology that has been around for more than 50 years. In the early days of the technology, the main application was compressed air leak detection. Even today, that is still the most widely used application for airborne ultrasound. Advancements in leak detection using ultrasound have come by way of reporting and documenting the air leaks that are found. The reports quantify the air leaks by showing the cost and CFM loss related to the air leak.
Over the years, through advancements in both ultrasound instrumentation and software, more maintenance and reliability personnel have begun to use ultrasound technology for more than just compressed air leak detection. Three applications in particular have seen a large increase in usage: condition monitoring of bearings and rotating equipment, condition-based lubrication using ultrasound, and electrical inspection of energized electrical equipment.
What is Ultrasound?
Ultrasonic equipment detects airborne and structure-borne ultrasounds normally inaudible to the human ear and electronically “transposes” them into audible signals that a technician can hear through headphones and view on a display panel as a dB level. On some instruments, incoming sound can also be viewed on a spectral analysis screen which shows either the FFT or Time Wave Form. With this information, a trained technician can interpret the bearing condition in order to determine what, if any, corrective action is needed, and the current data can be compared on the spot to the baseline data.
Ultrasound technology has many advantages:
- It can be used in virtually any environment
- Learning to use ultrasound technology is relatively easy
- The technology is relatively inexpensive
- Modern ultrasonic equipment makes it easy to track trends and store historical data
- Ultrasonic technology has proven itself to be extremely reliable in predictive maintenance, saving thousands upon thousands of dollars and hours of lost productivity
- There are remote monitoring options for both mechanical and electrical applications
Airborne and structure-borne ultrasound instruments are an extension of the user’s sense of hearing. Similar in that vibration feels what you can’t feel and infrared cameras see what you can’t see, ultrasound hears what you can’t hear. There are sounds taking place in a typical plant and manufacturing environment (machines running, production equipment running, etc.) that prevent us from hearing other sounds such as compressed air leaks, or electrical discharges like corona, tracking, or arcing. Ultrasound instruments listen for sounds that are not present in our normal audible range.
Typically, the sounds outside normal human hearing are high frequency sounds. The high frequency sounds are detected by the instrument and translated through a process called heterodyning into an audible sound that is heard in the headset by the inspector. The unit of measurement for sound is a dB level which is indicated on the display of the ultrasound instrument.
Why Remote Monitoring with Ultrasound?
Remote monitoring with vibration analysis and temperature has been available for many years. For ultrasound, it’s a fairly new addition to the technology’s repertoire of capabilities. When considering adding ultrasound to your condition monitoring program, the decision ultimately depends on what assets you would like to monitor. Once you have determined the assets that you would like to monitor, you need to identify the failure modes related to those assets. Understanding how those assets will fail will help you to determine which condition monitoring tool can be applied to find those failure modes.
Ultrasound is a proven technology that can detect certain mechanical and electrical faults much sooner than other technologies. By sensing subtle changes in ultrasonic amplitude, ultrasound is adept at finding early stage premature bearing faults. This is demonstrated by the I-P-F Curve:
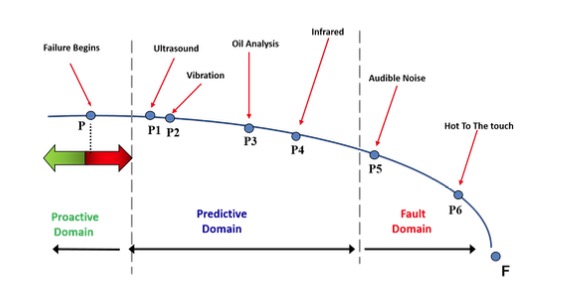
Ultrasound plays a critical role in helping to extend the life of bearings in the I-P interval by condition lubrication of bearings. Studies have shown that the majority of premature bearing failures can be attributed to lubrication. Whether it’s over-lubrication, under- lubrication, using the wrong grease for the wrong application, mixing incompatible greases, or lubricant contamination, all of it comes back to improper grease application. Ultrasound can prevent over- and under-lubrication, thus potentially eliminating a large number of bearing failures.
When a bearing lacks lubrication, there is an increase in friction. The higher friction also increases how much ultrasonic noise the bearing produces, indicated by a rise in the decibel (dB) level. While greasing a bearing that is in need of lubrication, one should see a gradual decrease in the dB level. Once the dB level has fallen back to a normal or baseline level, greasing can be ceased. If the bearing already has a sufficient amount of grease when greasing, then the dB level will slowly begin to rise as more grease is applied. That’s because over-lubrication also increases friction in the bearing housing, thus producing a higher dB level. The inspector would notice the rise in dBs as grease is applied and would stop greasing.
In the P-F interval once a failure has begun, ultrasound is excellent at finding it. These are bearing failures that can be detected even before changes in vibration. If you’re monitoring critical assets, ultrasound and vibration should be used together in an effort to potentially detect multiple failure modes that may be missed when using one technology alone.
Remote Monitoring – Mechanical Inspection
Remote monitoring of bearings and other rotating equipment with ultrasound can be done one of two ways:
The first is to use wired remote access sensors (RAS) which are mounted to the assets when it is safe to do so, and the cables brought out to a safe area (outside of guarding) where they can be connected directly to a portable hand-held ultrasound instrument. The cable lengths for the ultrasound remote access sensors can be made to lengths up to 100 feet or 30.48 meters.
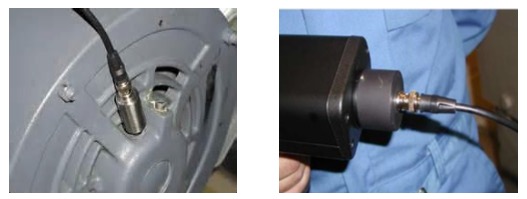
The other end of the RAS cable connected directly to a portable hand-held ultrasound instrument (right).
The ultrasound remote access sensors can also be connected to a junction box or switch box. As many as twelve ultrasound RAS’s can be connected to one switch box. Similar to the way vibration analysis switch boxes work, the ultrasound sensors are connected to the switch box, along with the hand-held ultrasound instrument. During analysis, the inspector turns the dial to the next point to collect a reading.
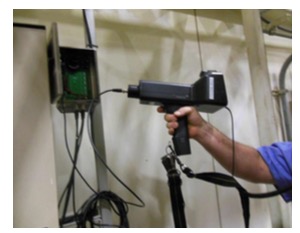
Remote monitoring with ultrasound can also be done continuously. For continuous monitoring with ultrasound, UE Systems offers a sensor called an Ultra-Trak 750. This is another stud-mounted sensor, but instead of connecting directly to a hand-held ultrasound instrument, this sensor has a 4-20mA output that allows for easy connection to existing plant process monitoring systems. An audio output also allows for sound recording for further diagnostics or comparing baseline sound files to alarm level sound files. Alarm levels and dB threshold settings can be used with the Ultra-Trak sensor that allow for alarm conditions to be noted and for trending potential problems over time.
Ideal applications for this sensor could include: high pressure safety relief valves, robotic applications, early warning of failure for a mechanical asset, flow disruption, and prompting a lubrication PM. The Ultra-Trak can also be wired into wireless transmitters to transmit the ultrasound data into existing monitoring systems. The wireless option may be ideal for areas that cannot be accessed due to safety, or areas that are hard to reach such as overhead cranes, bearings in wind turbines, robots, or remote assets away from the main plant or facility.
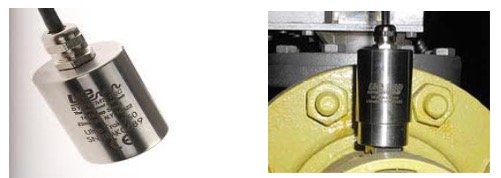
Remote Monitoring – Electrical Inspection
Ultrasound can be used to inspect almost any energized electrical equipment. This equipment may include metal-clad switchgear, transformers, substations, relays, and motor control centers, along with many others. Ultrasound can be used to measure equipment voltages from the low end (110 volts) to well over 12000 volts (12kV).
Traditionally, inspection of energized electrical equipment has been performed using noncontact infrared cameras; however, in recent years, ultrasound has been added to these inspections for various reasons. One of the main reasons has been for safety: An ultrasound inspection of electrical equipment can be done without the need to open the energized cabinet or enclosure. The hand-held ultrasound instrument is used to scan any openings on the cabinet. The high frequency sound produced by corona, tracking, and arcing from inside of the enclosure will exit through any of the openings. The inspector will hear the sound via the headset, and know that an anomaly is present. The sound can then be recorded to determine if the condition is corona, tracking, arcing, or some type of mechanical looseness.
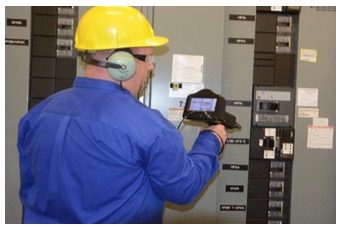
energized electrical equipment
Byproducts of the ionization process are ozone, electromagnetic emissions, ultraviolet light and nitric acid. Nitric acid is a corrosive and can deteriorate the insulators and connectors and lead to tracking and arcing.
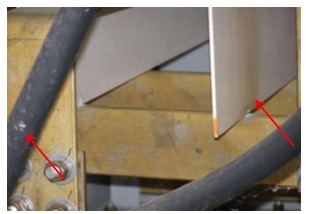
Notice the carbon deposit sand light brown discoloration of the insulation board on right.
When the sound file of corona is recorded, there are signature characteristics visible in the FFT and Time Wave Form (TWF) that will help to diagnose the condition. For corona, the discharge points only occur at the highest voltage point on the sine wave. This means that the amplitude peaks in the TWF are somewhat equally spaced as the discharges are only at the positive peak of the sine wave. The result will be well defined 60Hz or 50Hz harmonics.
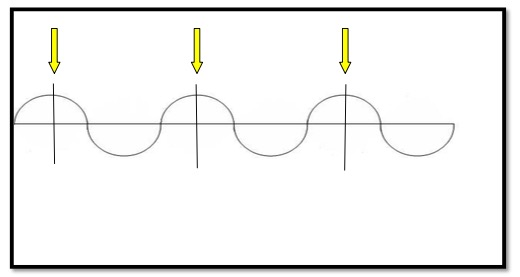
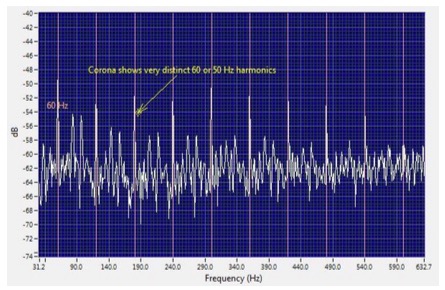
For tracking (low current pathway to ground across an insulator) and arcing (electrical discharge to ground across an insulator) there are also certain characteristics to look for. With tracking, the discharge does not have to take place at the peak of the waveform. Instead, it can happen anywhere on the positive portion of the cycle. The spacing of the peaks in the TWF would be similar, but not uniform. As tracking becomes more severe, there are more discharge events and therefore more non- uniformly spaced narrow peaks.
Arcing has the most non-uniform “look” in the FFT and TWF. Only the bursts of the discharge can be heard and these will be seen as wide peaks in the TWF view.
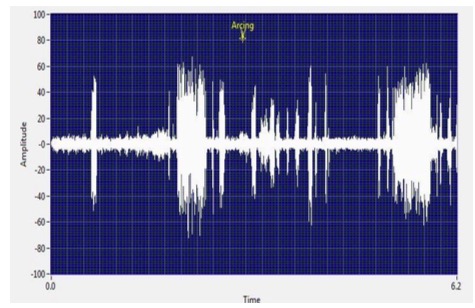
Remote monitoring with ultrasound is also easy to accomplish. UE Systems offers a remote mounted sensor for electrical inspection called an ECM (Electrical Cabinet Monitor) 586. Similar to the output of the Ultra-Trak 750, the ECM 586 also has a 4- 20mA output. There is also a heterodyned audio output to allow for sound recording. Analyzing recorded ultrasounds of electrical anomalies is the only way to diagnose with ultrasound the condition heard, whether it is corona, tracking, arcing, partial discharge, or some sort of mechanical looseness. The ECM 586 airborne ultrasound sensor can be mounted inside of an electrical cabinet such as a transformer or switchgear, and wired into the facility’s existing process monitoring systems or a PLC. The sensor will continuously listen for any abnormal electrical discharge that may start to occur such as corona, tracking, or arcing.
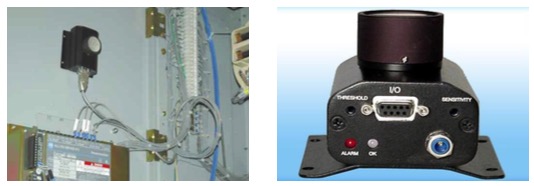
Remote Monitoring with Ultrasound – Conclusions
Remote monitoring with ultrasound is a viable option for maintenance and reliability programs that are already monitoring assets traditionally with hand-held devices, and for programs where ultrasound is currently not a technology that is being used. Because it is very complimentary to vibration analysis for mechanical inspection and infrared thermography for electrical inspection, ultrasound will only enhance condition monitoring efforts already in use.
Using ultrasound for mechanical and electrical inspection will deliver an increased level of monitoring for critical assets and assets that are currently not being monitored with vibration analysis or other condition monitoring technologies. Anywhere you would consider using traditional data collection techniques, remote monitoring can be a viable option as well. In areas that are inaccessible, dangerous, or remote, remote monitoring with ultrasound may be your only option. Additionally, a multi-technology approach to condition monitoring increases your chances of finding multiple failure modes and detecting them early enough to make the necessary repairs before they become catastrophic.