Rodney J. Scott, President
Level III Infraspection Institute Certified Infrared Thermographer® & Instructor
Invizions, Inc.
2519 State Route 61Norwalk, Ohio 44857Ph: 419-663-8621 www.invz.net
Abstract
Fugitive gas emissions represent a significant liability for companies in the form of cost, safety, and potential environmental contamination. In addition to the unwanted loss of product, hefty fines from regulatory agencies may also apply. Under proper conditions, thermal imaging may be used to remotely detect evidence of a wide variety of gas leaks including sulphur hexafluoride (SF6) and ammonia. This paper will discuss this application in detail including proper selection of thermal imaging equipment, inspection techniques, and helpful hints to correctly identify and label various leaks.
Introduction
Fugitive gas emissions are emissions of gases or vapors from pressurized equipment due to leaks and various other unintended or irregular releases of gases, mostly from industrial activities. As well as the economic cost of lost commodities, fugitive emissions contribute to air pollution and climate change.
Leaks from pressurized process equipment generally occur through valves, pipe connections, mechanical seals, or related equipment. Fugitive emissions also occur at evaporative sources such as waste water treatment ponds and storage tanks. Because of the large number of potential leak sources at large facilities and the difficulties in detecting and repairing some leaks, fugitive emissions can be a significant portion of total emissions. Even though the quantities of leaked gases may be small, leaks of gases that have serious health or environmental impacts can cause a significant problem.
To minimize and control leaks at process facilities operators carry out regular leak detection and repair activities. Routine inspections of process equipment with gas detectors can be used to identify leaks and to estimate the leak rate in order to decide on appropriate corrective action. Proper routine maintenance of equipment reduces the likelihood of leaks. This report highlights new thermal imaging techniques to locate and document fugitive emission leaks in ammonia (NH3) related equipment.
OSHA Standards & EPA Liabilities
In 1992, the OSHA standard “Process Safety Management of Highly Hazardous Chemicals” (PSM) was issued in the Federal Register. This standard was developed to give requirements for the management of hazards associated with processes using highly hazardous chemicals to help assure safe and healthy workplaces. For refrigeration systems, the standard applies to systems that contain 10,000 pounds of ammonia, although multiple systems that are not interconnected, that have less than 10,000 pounds each may still be covered under PSM due to the proximity of the systems. A careful review of multiple systems must be done to determine the appropriate action to take in the PSM standard. Any facility having the threshold quantity of ammonia must have a PSM program in place, as of May 1992. All new facilities are required to develop a plan and have it in place prior to introducing ammonia above the threshold quantity.
The PSM standard contains the following fourteen elements:
-
Process Safety Information (PSI)
-
Process Hazard Analysis (PHA)
-
Standard Operating Procedures (SOP)
-
Employee Participation
-
Training
-
Contractors
-
Pre-Startup Safety Review
-
Mechanical Integrity (MI)
-
Hot Work Permit
-
Management of Change (MOC)
-
Incident Investigation
-
Emergency Planning & Response
-
Compliance Audit
-
Trade Secrets
Risk Management Program (RMP)
In June 1996, the Environmental Protection Agency (EPA), in accordance with the Clean Air Act Amendments of 1990, issued the “Risk Management Program for Chemical Accidental Release Prevention” (RMP). The goal of this regulation is to prevent accidental chemical releases and to minimize their impact. The focus of the RMP regulations is protection of the public and environment from the effects of an accidental release of highly hazardous chemicals. All ammonia refrigeration systems containing 10,000 pounds or more must meet the requirements of the RMP regulations. Implementation of the RMP was required by June 1999.
The RMP has the following major elements:
-
Management System for the RMP
-
Offsite Hazard Assessment and Consequence Analysis
-
Including Five Year Accident History
-
Accident Prevention Program
-
Emergency Response Program
-
Submit Plan to EPA
Note: The OSHA-PSM and EPA-RMP, although different in some respects do have several common elements. These common elements do not have to be duplicated, but can be implemented for each program.
Examples of Fines Imposed by the EPA
Tanner Industries, an East Providence, RI company that distributes ammonia, faces a $149,080 penalty for violating federal regulations meant to prevent chemical accidents, according to a recent complaint by the U.S. Environmental Protection Agency.
Tanner operates ammonia distribution facilities across the country, including one in East Providence, and is subject to the Clean Air Act’s risk management planning requirements because ammonia is an extremely hazardous substance. Although Tanner has a risk management plan, EPA’s New England office is proposing to fine Tanner for a deficiency in its plan concerning the failure to anticipate the problems that could arise if an ammonia release occurred at the East Providence facility during periods when the facility is unstaffed. In a separate administrative order issued in June 2009, EPA New England ordered Tanner to correct these deficiencies, and Tanner is cooperating, according to the EPA.
According to the complaint filed by the EPA, Tanner failed to do the required analyses or take precautions to address the fact that its facility is not routinely staffed except when ammonia is being actually received or distributed. For instance, Tanner failed to consider the use of sensors or monitors to detect leaks of ammonia or conditions that might lead to leaks. Tanner’s emergency response program also did not include adequate communication and coordination with local emergency response agencies, and the company’s plan did not ensure that the public would receive adequate notice of an accidental release (article taken from the Reliable Plant website:http://reliableplant.com/Read/26877/Tanner-EPA-fine-violations.
EPA Fines Oregon Freeze Dry for Failing to Report Ammonia Release
Apr 27, 2011 Oregon Freeze Dry Inc. will pay the U.S. Environmental Protection Agency $3,323 for its failure to report an estimated 422 pounds of anhydrous ammonia released at its food freeze-dryer facility in Albany, Ore. In addition to the penalty, the company agrees to spend at least $19,435 to purchase and install an ammonia detection and alarm system and a remote and automatic shutdown valve system that would activate in the event of a release. On November 22, 2009, the Oregon Freeze Dry facility released approximately 422 pounds of ammonia into the environment at its facility located at 525 25th Ave. SW in Albany, Ore., according to the EPA settlement. The facility is the largest diversified food freeze dryer in the world and uses large quantities of anhydrous ammonia as a refrigerant at its facility.
Toxic Ammonia Cloud In San Jose – Company to Pay $75,000 in Fines for Crimes Related to Release
A refrigeration business pled guilty in Santa Clara County Superior Court today to negligently causing a release of toxic gas and not calling 9-1-1 to report it.
Judge Patrick Tondreau imposed a $75,000 fine on the defendant, Modern Ice and Cold Storage, which uses anhydrous ammonia at its facility on Oakland Road. Modern Ice was convicted of breaking several laws designed to protect workers and the public from the worst kinds of chemical accidents.
On May 8, 2001, anhydrous ammonia escaped from Modern Ice through a corroded valve and two open pipes that should have been closed. The invisible vapors saturated the neighborhood with a pungent odor that sent four people to the hospital. Although the injuries in this case were minor, ammonia is a toxic gas that can cause breathing problems, eye damage, skin burns, and death.
Two Modern Ice employees, who were aware of the leaking ammonia but did not call the fire department, pled guilty to the charge. The court sentenced each to perform 50 hours of community service and to pay a $1,000 fine (http://www.sccgov.org/)
Imaging Equipment
Thermal imaging cameras find greenhouse gas emissions or volatile organic compounds (VOCs) and are unbeatable for detecting even the smallest gas leaks.
Detectable Gases at Minimum Detected Leak Rate (MDLR)
1-Pentene – 5.6g/hr |
Benzene – 3.5g/hr |
Additional Gases with no Required MDLR
Anhydrous Ammonia (NH3) |
Carbon Monoxide (CO) |
Inspection Techniques
Inspection techniques will vary depending on the type of gas, process , and environmental conditions. Inspections require the following conditions: clear line of sight, equipment under load, and a qualified assistant with process knowledge and clear understanding of all safety equipment.
Documentation Requirements for Qualitative Analysis
Qualitative infrared thermography is the practice of gathering information about a structure, system, object or process by observing images of infrared radiation, and recording that information.
Qualitative analysis reports should consist of the following:
1) Thenameandvalidcertificationlevel(s)annumber(s)oftheinfraredthermographer.
2) Thenameandaddressoftheenduser.
3) The names(s) of the assistant(s) accompanying the infrared thermographer during the inspection.
4) Themanufacturer,modelandserialnumberoftheinfraredequipmentused.
5) A description of the location and construction of the facilities that were inspected and notations of any portions that could not be inspected.
6) Thedate(s)oftheinspectionandwhenthereportwasprepared.
7) Adescriptionoftheexceptionincludingisexactlocation.
8) Thetimetheexceptionwasdocumented.
9) The weather conditions surrounding the exception including the inside and outside air temperatures, wind speed and direction, and the sky conditions.
10) Hard and/or digital copies of thermal image (thermogram) and corresponding visible-light image of the exception. When approved by the end user, the infrared thermographer may provide sketches or drawings in place of, or in addition to, thermograms and photographs.
11) The field-of-view of the infrared camera lens.
12) Notation of any windows, filters or external optics used.
13) Any other information or special conditions which may affect the results, repeatability or interpretation of the exception.
14) The distance from the infrared camera to the exception.
15) The emissivity, reflected temperature and any transmittance values used to calculate the temperature of the exception.
16) The surface temperature of the exception and of a defined reference, if applicable.
Conclusion
Protecting the environment, our health, and equipment is more important than ever before. Various environmental and health conscience agencies are implementing procedures to protect us and fine for negligence. Properly trained thermographers with the right equipment have the ability to head off various fugitive gas emission problems. Proper leak detection, identification and documentation will not only contribute greatly to “Process Safety Management” and ” Risk Management Programs” it will reduce the cost of product loss and increase profits. Thermal imaging equipment with these capabilities is expensive but you don’t have too look far to find properly trained and certified technicians and service companies to perform annual surveys at a fraction of the cost.
Sample Images
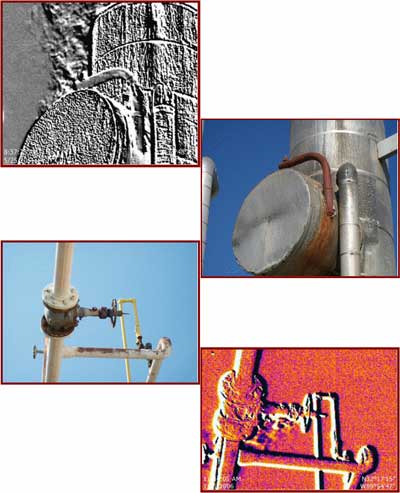
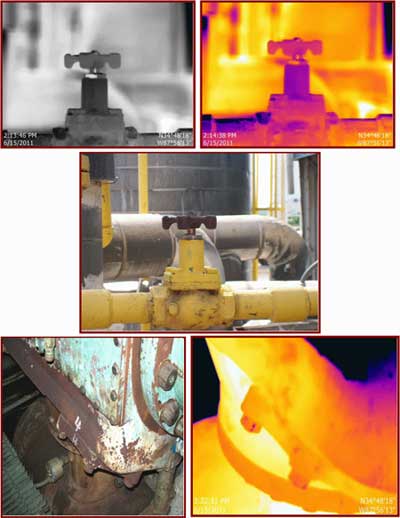