Gregory R. Stockton, President
Stockton Infrared Thermographic Services, Inc. & United Infrared, Inc.
8472 Adams Farm RoadRandleman, NC 27317Ph: 888-SCAN-4-IR
Abstract
Eleven years ago, the author published “NOT the low hanging fruit of Infrared Thermography” – a white paper discussing why thermographers should explore the many other upcoming applications for infrared…other than the electrical application. Since then, many changes have occurred in the world of infrared (IR) and particularly in electrical infrared…most of them good. To date, IR testing of switchgear remains the most popular infrared application.
This paper discusses the market forces, insurance requirements, government regulations and risk management thinking that are changing the electrical testing industry in general, and the electrical infrared testing application in particular.
Introduction
Today’s infrared thermographer has many opportunities. Just about anything can be imaged and successfully analyzed using infrared thermography as long as the thermographer has the right equipment, knows how to use it, and can figure out how to analyze it. It seems the only real limitation is the thermographer’s imagination and their ability to get someone who needs the information to pay for it.
The popularity of a given application is tied to individual markets by:
-
the point of development of IR technology at that time
-
the amount and quality of recent advertising a particular application has received
-
the perceived need of that particular application at that moment
-
the relative cost of doing the survey vs ROI (return on investment)
All applications of IR thermography have gained popularity over the past thirty years and continue to become more popular, now at an exponential rate.
As each class of IR cameras reaches a new lower benchmark price point, new sets of markets open. This has had a big impact on the electrical infrared testing market, along with every other application. The main reason is competition between manufacturers and because of manufacturing, technical and marketing economies of scale. The thermal imaging industry is experiencing tremendous growth. The camera manufacturers are now producing thousands and thousands of cameras, creating commodity pricing. Again, as the price drops, more new markets open, the cameras become cheaper to make, and the price drops.
Why and How We Do What We Do
By now, almost everyone in facilities management knows that infrared surveys of electrical switchgear are absolutely an integral part of every preventive maintenance (PM) and predictive maintenance (PdM) program in every facility. As infrared thermographers, our purpose is to reduce our client’s business loss risk by reducing the risk of premature failure of electro-mechanical components. These failures create a danger to people, cause the loss of equipment and result in downtime of the operation of the facility. With respect to electrical equipment, the reason for performing an infrared survey is to find electrical faults before they fail, hence it is predictive maintenance. Faults need to be found in their nascent stage, before damage has occurred and especially before component failure, so that maintenance personnel can repair them.
The infrared technique is predicated on the fact that:
-
There is a locked relationship between temperature [rise] and resistance in electrical components and between temperature [rise] and friction in mechanical components, etc., and
-
Infrared thermography can accurately detect heat and heat patterns on the surfaces of these components.
Common reasons given for performing infrared surveys of electrical switchgear:
-
reduce downtime from electrical failures
-
increase electrical and mechanical equipment service life
-
comply with insurance requirements and government regulations
-
lower maintenance and repair costs
-
prevent catastrophic failures
-
lower risks from arc flash
Market Forces, Camera Sales and Proper Training
With the better quality and cheaper prices of modern infrared cameras, software, and computers, infrared thermographers of today are almost never limited by equipment costs, or their ability to measure temperatures or discern differences in temperature. Rather, they are limited by their knowledge of how hot the object that they are surveying should be, what to report (and what not to report) as a fault, and how to rate the finding. Just about anyone can turn on an imager and shoot a picture of a piece of switchgear. Knowing what conditions are important, when to perform the survey, how to evaluate imagery and what to report and not to report, is not all that easy. Then there is the issue of accurately measuring temperatures. This is why professional thermographers save companies millions of dollars.
This is also where market forces, camera sales and proper training come into play. Infrared camera salespersons have an obvious incentive to make the sale. Once they get past justifying the initial cost of the camera, the sales objections become: a) the ease of camera and software operation, b) the cost of training, and c) the cost of time allocation for surveying and reporting. Especially with respect to the under $10k class, these cameras are exceedingly easy to operate. With a quick on-line webinar, one-hour demonstration and a couple of 8-hour practice sessions, the function of all of the buttons is mastered. The rudimentary image processing and reporting software is also pretty easy to learn as well…those objections are quickly overcome.
I am only referring to electrical scanning here, not all the other applications and not even mechanical scanning.
The tough objection to handle is “how long will it take, how many mistakes will it take, and how much will it cost, before the thermographer gets up to speed?” This is a painful question for the potential buyer, because it goes to the heart of the sale – “should we do infrared on our own or should we sub it out to a professional thermographer?” Recent market forces have changed things.
Prices for IR cameras have dropped to a point where the professional IR camera salesperson can hardly afford to make these low-dollar sales calls. Since visiting the site and looking over the operation, reviewing all the aspects of which type of camera, which model, which features would be best, how the camera will be used, etc., and making customized recommendations to the facilities management, takes more time than it is worth – especially if the potential client could then just go on-line and buy the camera from a web site. Most of the people who now sell these cameras (distributors / retailers) are selling them as a commodity, at commodity prices. So naturally, the sale has become about price, and salesperson’s proclivity is to downplay the issues of competency, the true cost of setting up an infrared PdM program and all the questions above with respect to the camera fit. The fact is that infrared thermography requires professional advice at all levels. The trade-off is price for advice.
To go in-house or contract it out, that is the question. It is no longer an issue of expensing the camera, or even the price of a couple of week-long certification training classes and the time away from other tasks. The issue is the getting up to speed and not making too many expensive mistakes during the learning process. Success in IRt is not about the camera, it is about the quality of training and level of experience of the person behind the camera. A good rule of thumb is if a company plans to do less than twenty days a year of electrical infrared thermography, it makes no sense to have an in-house program, even if they are given an infrared camera for free. Even if the camera is used twenty-plus days a year on electrical gear, it is not worth the investment if it is only used for that one purpose. Why go through the steep learning curve if the potential thermographers will not be doing other applications in the facility? Electrical and mechanical troubleshooting should be the #2 use, after regular surveys. Next, all the other uses should be considered, like finding water leaks and heat loss, mapping moisture in building roofs, improving manufacturing processes and product R&D. If the camera is only going to be used for one month a year (30 days), that means it will sit in a box, waiting to be lost, broken, or stolen, for 11 months.
Many times a company requires or prefers a third party do the work, but after multiple days, for most operations, it starts to make sense for a company to get into IR itself. So once a company has made up its mind to go with an in-house program and has made a camera purchase, the hard part begins. Making the costly mistakes of under-reporting and over-reporting can be minimized by hiring a professional thermographer to go with the electrician for a couple of weeks at the beginning and being available for expert consultation.
A good candidate will have knowledge of the objects that are going to be examined, good computer skills and the willingness to learn thermodynamics and physics. Obviously, an electrician that understands electrical switchgear has a leg up to becoming an electrical infrared thermographer. The best thermographer candidate is intrigued with the technology, someone who is a self-starter, one who likes to discover new techniques, explore where nobody has been and is not scared to be wrong. This is 20+ years of training thermographers writing this…if you give an infrared camera to an undertrained, timid or uninterested person, you will be looking for someone else in less than 90 days.
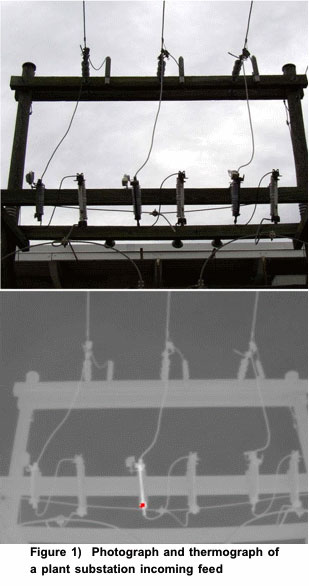
Of Safety and Government Regulations
All exposed electrical circuitry in all buildings must be in an enclosure of some type and since infrared imagery shows surface temperatures and only surface temperatures, all electrical panel covers must be removed to be successfully surveyed. If the panel cover cannot be removed while energized, the manufacturer will have designed it that way. For those panels, IR windows are a great option as they allow for safe viewing of electrical switchgear through a port that is mostly transparent in thermal infrared wavebands. If the panel cover can be removed while energized, proper personal protective equipment (PPE) must be used. In most areas of the US, NFPA 70 is the Electrical Code. NFPA 70B is the recommended practice for electrical equipment maintenance (infrared is recommended). NFPA 70E is the standard for electrical safety in the workplace. These are all written and sold by the National Fire Protection Association. NFPA 70E has been adopted by OSHA and we believe the insurance industry will follow. By and large, the corporations (at least officially) have adopted the NFPA documents, even if it is not required by every municipality or followed religiously in the real world. But, ultimately, the building owner is responsible for safety in their own facilities. These changes over the past ten years are all good for infrared thermography and mean more scanning than ever will be taking place moving forward.
How much money does infrared surveying save the typical operation? It varies wildly by building design, building use, maintenance practices, etc. The true ROI of performing infrared surveying, as compared to the cost of other maintenance has been impossible for me to find all these years. Also, data on how many people are hurt or killed each year while performing IR surveys, how many thermographers are following NFPA 70E to the letter, or how many people are killed by following NFPA 70E…all remain mysteries. There is little hard data available on how much money has been saved by building owners doing IR, although there has been no shortage of case studies presented over the years by thermographers. While these case studies are great for marketing purposes, they have little actuarial value.
Now, following accepted practices:
-
In order to perform an IR survey, the panels have to be marked with a rating letting the thermographer know what PPE is required at a given distance.
-
In order to know the rating, an arc flash survey has had to have taken place.
-
In order to do an arc flash survey, one-line diagrams need to be updated.
-
In order get accurate one-line diagrams, an electrical engineering study needs to be completed.
As one could imagine from the above, some managers have chosen not to perform arc flash or IR surveys because if they have no updated one-lines and if it is going to cost thousands of dollars to get their paperwork together…it becomes easier not to do it. But is that less risky? Almost all operations are somewhere in the middle between compliance and non-compliance and the number of infrared surveys of electrical switchgear continues on an upward trend line. Since reducing risk is becoming a corporate priority, facility managers are actually willing to pay more to do a proper infrared job and do it safely. Where the average price of an average infrared survey has gone down somewhat over the past ten years, pricing for high quality electrical surveys has remained the same.
Risk Management and the Insurance Industry
Insurance companies are requiring more infrared testing every day. In fact, it is hard to find a building larger than 100,000 square feet that is not supposed to receive an electrical infrared survey at least once every three years. They must know the numbers referred to above, even if they are not sharing. They ought to know, since [other than managing investments] managing risk is the business of every insurance company. The Property & Casualty and Boiler & Machinery carriers are the most interested in predictive maintenance and minimizing loss of facilities and equipment. Some have even created their own infrared groups to perform the surveys of their insureds’ operations and facilities. Contrary to what some maintenance personnel think, these surveys are not “free” from the insurance company… nothing is free. The costs are passed on to the insured, but it is still good because the IR survey will reduce losses, saving the insurance company and the businesses money. In corporations, the power/influence pendulum has swung over the last ten years, in favor of the risk managers by result of the fine work of many attorneys. Implementing risk management has high costs, but based on the reduction in liability that they now enjoy, the companies are willing to pay for it.
The Future of Temperature Monitoring of Electrical Switchgear
My prediction is that infrared testing of electrical switchgear will be around for a very long time, but there are much safer and much better ways for electrical switchgear to be monitored for temperatures than having an electrician open a panel and a thermographer look at it and analyze it. Eventually, all monitoring of electrical switchgear will be done remotely and automatically, without human danger, subjectivity, and error. I see a time in the not so distant future (~20 years) when all critical electrical equipment will have within its bowels, a tiny remote high resolution thermal imager monitoring each pixel’s temperature. The manufacturers will install the thermal imager along with other monitoring devices, first as an option, then as standard equipment. The switchgear and its individual components will have their own IP address, sending steaming data about its physical condition 24/7/365 to a computer with an algorithm to alert facilities management of impending failure, eventually predicting when temperature, load and ambient conditions warrant corrective action, which action should be taken, and when.
But for now, we have two ways that will take us forward to the ultimate automatic infrared thermography device of the future:
-
Infrared viewports, or IR windows, which are installed on panel enclosures, adjacent to internal components, allowing the thermographer to safely see into the switchgear – a good example being “IRISS Windows”, developed by IRISS, Inc. (www.iriss.com).
-
Self-contained temperature monitoring sensors, which are attached to electrical enclosures, measuring the difference in temperature between the internal temperature and ambient temperature – a good example being “Delta T Alert”, developed by Delta T Engineering, LLC. (www. deltatengineering.com).
Conclusion
Thermographic electrical switchgear testing is still the “low-hanging fruit” of IRt, as popular as ever, growing in use as the technology becomes more of a commodity, with commodity pricing of the cameras and eventually the service. The short-term challenge mainly comes from safety protocols. Other applications of IRt do not, and will not compete with electrical switchgear infrared testing; instead, by association make it more popular, until the technology becomes so well-developed that thermography of electromechanical devices is done primarily by artificial intelligence.
Author Biography
Gregory R. Stockton has been performing electrical IR surveys for over twenty-two years. He is one of the technical directors for ElectricIR.com, an international network of electrical infrared thermographers. Greg is a principal in three infrared companies; Stockton Infrared Thermographic Services, Inc. (www.StocktonInfrared.com), United Infrared, Inc. (www.UnitedInfrared.com) and RecoverIR, Inc. (www.RecoverIR.com). He is a Certified Level III Infrared Thermographer with thirty years of experience in the construction industry, specializing in maintenance and energy-related technologies. He has published many technical papers on the subject of infrared thermography and numerous articles about applications for infrared thermography in trade publications. Greg is a member of SPIE (the international society of optics and photonics), a member of the Thermosense Program Committee, past Chairman of the Buildings & Infrastructures Session and Co-Chairman of Thermosense, at the Defense, Security and Sensing Symposium.