Level III Infraspection Institute Certified Infrared Thermographer®
Infraspection Institute
425 Ellis Street
Burlington, NJ 08016
Tel. 609-239-4788
www.infraspection.com
Introduction
With green awareness at an all-time high, facility managers are constantly on the lookout for new ways to save money and energy while reducing their company’s carbon footprint.
One of the best opportunities for detecting excess energy loss is steam trap testing. Although defective steam traps can waste thousands of dollars annually, their maintenance is often overlooked. Presently, estimates for steam trap failures within industrial facilitites is 50%. Considering that medium sized facilties can have hundreds of traps, the potential for energy savings is considerable.
In order to understand how infrared thermography is applied to steam trap inspections, we first need to understand the steam system itself.
In most plants, steam is produced in a power plant with a boiler. This allows the majority of heat energy to be produced in a central location. The steam is then piped throughout the facility via steam lines to locations where heat energy is needed. In many cities, steam may be purchased from local utilities. Regardless of the source, steam is expensive and preventable losses are unacceptable.
Steam is an odorless, colorless, tasteless gas which forms when water is heated above 212°F (100°C). In a pressurized system, steam is capable of storing and transporting large quantities of energy. Once steam has formed, more energy can be introduced by further heating. This causes both its temperature and pressure to rise.
Once steam leaves the boiler, it begins to lose energy and cool. As its temperature falls, the steam condenses back into water. Failure to remove condensate from the steam system sets up a vicious cycle.
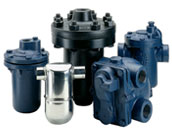
Armstrong International
When condensate forms, the overall temperature of the remaining steam drops, causing the steam to condense at an exponential rate, greatly reducing the efficiency of the steam system to transport energy. In turn, this temperature drop causes more steam to condense causing a further temperature drop. If left unchecked, this process will continue until all steam has returned to water. In order to maintain optimum steam system performance, steam traps are used to remove condensate from the system.
Simply put, steam traps are automatic mechanical valves designed to discharge condensate and air from the steam system. Steam traps come in a variety of styles. The style of trap used depends upon the application of the steam system. Some of the more common styles are:
- Inverted Bucket
- Thermodynamic (Disc)
- Thermostatic (Bellows)
- Float
- Float and Thermostatic
Like all mechanical devices, steam traps eventually fail. Failure in an open position allows costly steam losses to add up quickly. Failure in a closed position not only reduces steam system efficiency but also allows acidic condensate to attack steam system components. Visually, failed steam traps usually exhibit no unusual symptoms.
According to some industry estimates, steam trap failures can run as high as 40% at a given facility. Such a high failure rate, combined with the high cost of steam production, can account for losses exceeding several hundred thousand dollars annually.
To date, steam trap testing has most often been accomplished by either thermographic inspections or by ultrasonic testing. Each of these methods has its merits; however, each has its limitations.
Thermographic inspections traditionally measure both the inlet and outlet temperatures of the trap to determine the temperature difference (delta-T). While this technique may be somewhat effective for some of the simpler trap designs such as disc traps, it does not work well for the more complex traps such as float and thermostatic traps. It also does not work well for traps where condensate load constantly changes or where several traps in close proximity discharge into a common condensate line. Delta-T temperature measurement is a crude indicator of trap condition as small to moderate leaks may not be detected.
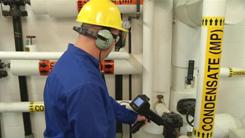
UE Systems
Ultrasonic testing employs an ultrasonic translator to actually listen to the trap operate. The ultrasonic translator uses a contact probe to detect ultrasonic frequencies (above 20 kHz) in the trap and translate these frequencies into sounds that an operator can hear. Like thermography, ultrasonics is a non-destructive, on-line test that requires no system shutdown. Typically, ultrasonic translators are very sensitive and can detect traps that are just beginning to leak steam. However, ultrasonic translators cannot detect “quiet” failures such as traps failed in the closed position, air locked traps, or steam traps not under load.
Most ultrasonic translators are fairly simple to operate; however, experience is necessary to accurately interpret results. By incorporating both thermography and ultrasonic testing together, the limitations of each method are overcome and a highly accurate inspection technique is realized.
When using both ultrasound and thermography to inspect steam traps, the thermal imager is first used to measure the inlet pipe (uninsulated) temperature at the trap. The inlet pipe temperature should be close to the system’s steam temperature, which indicates that live steam is reaching the trap and that the trap is neither air locked nor failed in the closed position.
If inlet pipe temperature is significantly less than steam temperature, steam is not reaching the trap and investigation as to the cause is necessary. Most often this is due to an upstream valve being closed; however, pipeline obstructions may also prevent steam from reaching the trap. Thermalimagers are particularly well-suited to quickly locate closed valves or steam line blockages.
Once it has been determined that steam is reaching the trap, the ultrasonic translator is used to listen to the trap operate. Properly working traps are generally quiet except during cycling. Typically, a hissing or rushing sound indicates a failed trap. Trap cycle time, trap orifice and air vent can also be checked. In cases where several traps are located in close proximity, each trap can be accurately tested on an individual basis.
Like other types of non-destructive testing, results will depend upon operator training, experience, and test equipment. Quality test instruments as well as thorough knowledge of steam system operation will help to ensure accurate results and tremendous cost savings.