How to Use Reliability to Offset Supply Chain Issues
Noah Bethel, CMRP
Vice President, Product Development
PdMA Corporation
5909-C Hampton Oaks Parkway, Tampa, FL 33610 USA
Office: 813.621.6463 ext. 124 | Fax: 813.620.0206
www.pdma.com |
With recent COVID-related shutdowns of supply lines that have crippled companies, investing in reliability becomes a vital strategy for keeping systems and production lines running. Without parts, companies cannot manufacture products or repair machinery when it breaks. In such an environment, making sure existing equipment runs for as long as it can is the smartest investment a company can make, resulting in fewer unexpected failures and unplanned outages. By limiting the occurrence of breakdowns, companies can maintain parts inventories and continued manufacturing throughput.
Reliability is the application of knowledge and technology to identify correctible conditions that would otherwise lead to failure, thus extending the life of a company’s assets. Having a machine reliability program can make the difference in preventing a shutdown to key systems during periods of supply chain shortages. Too often, companies will operate under a reactive or run-to-failure mindset, especially when equipment is cheaper to replace than repair, or cannot be repaired. Though this is a legitimate strategy for some types of assets, it is considerably less so for high-cost assets that are complicated to repair. That is why when supply chain issues surface, it becomes even more disruptive since there is no longer a means of replacing key equipment in the short term.
Supply Chain Issues and Their Effects
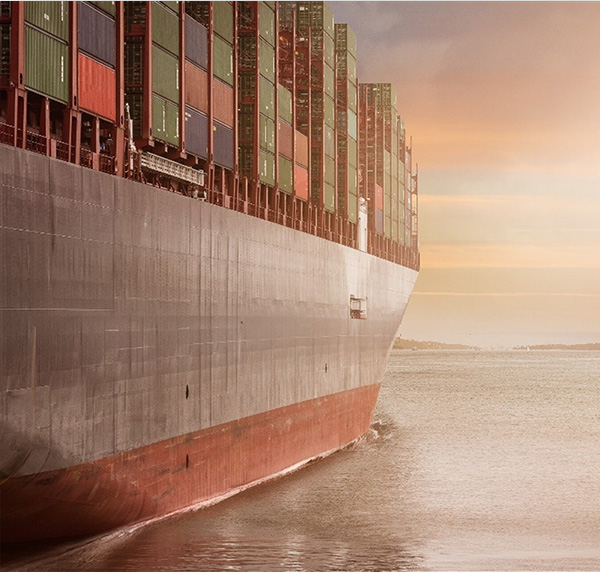
Recent news stories related how hundreds of ships were without available berths in ports along the West Coast creating a serious disruption in the availability of both the parts needed to create new products and the parts needed to fix machinery used to manufacture such new products. Despite government countermeasures such as keeping ports open twenty-four hours a day, seven days a week, the lack of available truck drivers or the bottleneck inefficiencies of the port processes have impacted port recovery. Companies have been experiencing backlogs for ordering parts with pending available dates that stretch over a year or more, even from suppliers who had been previously vetted for trustworthiness. Often, the links run deep and just one critical part can ripple through the manufacturing ecosystem, a supplier’s supplier runs out of a part, and it affects everyone else downstream.
These shortages are already influencing the availability of goods during the 2021 holiday season, often causing sharp price increases which further affect supply chains. A recent study by the U.S. Census Bureau reported nearly sixty percent of businesses were experiencing supply chain issues in August, and this problem has become even more visible since1. It is uncertain when supply chains will return to a degree of normalcy, with some experts believing it will take until the summer of 20222.
Aside from these recent issues, supply chains are always subject to a variety of disruptive conditions, such as unplanned information technology outages, adverse weather conditions, cyber-attacks, and other transport network disruptions3. Any one of these conditions could generate unplanned bottlenecks in a supply chain, and none of these are outliers. Additionally, most of these disruptions could be considered a disaster, even though recovery will occur eventually. When a true disaster or catastrophe occurs, existing networks are destroyed and need to be rebuilt, which takes even more time and often requires assistance from governments. Hence, a run-to-failure policy is a gamble on stable economic and climatic conditions.
A focus on reliability could mitigate some of these issues, particularly where it comes to fixing potential failures in equipment before they occur, alleviating the need for repair parts that might not be available for many months. For instance, electric motors have well-known fault zones that if detected and resolved early enough can extend the life of this costly piece of equipment.
Investing in Electric Motor Reliability
Investing in motor reliability means investing in equipment that can detect anomalies in motors before they become problems. Too often, when a motor begins to fail audibly or becomes overheated, things have progressed far along the P-F curve. The farther along on the P-F curve, the more costly a repair is likely to be.
The primary goal of reliability is to keep motors running at optimal health, diminishing the need for costly, hard-to-find replacement parts. Using available technology, companies can test for faults, whether there is an imbalance, a power quality issue, or something detectable in the system harmonics. When detected early, a system can be cleaned up and the life of the motor extended, which is often the more efficient and less costly route.
Having reliable equipment removes any potential bottlenecks from the manufacturing process and allows companies to focus on other issues. The issues that electric motors run into are very predictable and arise from six known fault zones.
Fault Zone Analysis
Fault zone analysis uses online and offline assessments to measure and detect the status of potential problems in electric motor functions. The six fault zones4 are power quality, power circuit, insulation, stator, rotor, and air gap. Here is a quick recap of these six fault zones5:
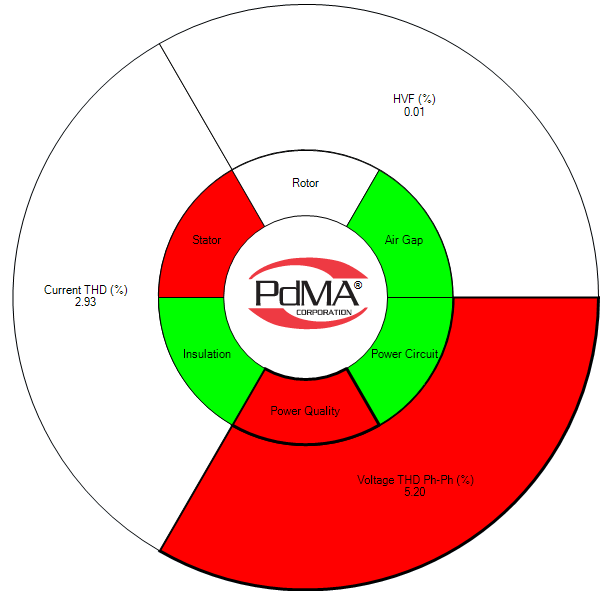
- Power quality. What is fed into a system affects how the system reacts, much like the adage “You are what you eat.” When bad power quality is fed into a system it can lead to premature failure of the system.
- Power Circuit. Even with a solid power supply, if the connections delivering the power to the motor are faulty or deliver less power than expected to the motor, conditions are set for failure, just as with the power quality.
- Insulation. Current that is fed into the motor goes through the windings, creating a magnetic field. Proper insulation prevents this current from going to ground. Faulty insulation could result in causing motors to trip or even cause fires.
- Stator. These are the windings in the motor, the stationary element that the rotor turns in. Faults in the stator could be comprised of an event like a turn-to-turn insulation fault, where windings touch each other prematurely, causing the motor to trip or overheat, much like insulation failures.
- Rotor. A variety of faults can occur in the rotating element of the motor. For example, high resistance connections on a rotor cage or the steel laminations can start to fail.
- Air Gap. Problems can arise between the gap between the stator and the rotor. A 2,000-horsepower motor, roughly the size of a car, might have a shaft turning nearly 3,600 rpm and an air gap measured in millimeters; this requires a high level of precision and balance.
Knowing these six fault zones helps open more discussions between electricians and non-electricians, beyond a simple, “Something is wrong with the motor.” It facilitates a deeper discussion to pinpoint the problem and to be able to communicate that problem to all interested parties in the organization. By monitoring these six fault zones, a reliability team can maintain motors in an optimal condition, reducing the need for repair parts.
The Impact of Reliability on Efficiency
Reliability allows companies to weather fluctuating supply chain conditions, keeping machines running and maintaining profitability. Predictive maintenance has the potential to be more cost-effective than preventive and reactive strategies, but it does require an initial investment and an in-depth knowledge of the company’s assets, not to mention more extensive planning.
Also worth considering, with the enormous amounts of electricity needed to keep these motors running, making sure they run efficiently has other beneficial effects. An efficient motor reduces power usage and cost less to operate. This can have an impact on environmental concerns as well, even in less obvious ways such as reducing the need for repair parts and all the associated power costs associated with producing them. Depending on the political flavor of the day, high-efficiency standards can influence the decision-making regarding repairs or replacing lower efficiency motors. This may not have as substantial an impact on larger companies, but smaller companies could find themselves unable to compete when efficiency standards become costly to implement.
It is also important to note where gaps can occur in a reliability program such as in quality control, trending, and troubleshooting6. Here is a quick summary of these potential gaps:
- Quality Control (QC). Often gaps in QC are the result of underlying assumptions, such as assuming a newly installed piece of equipment will run perfectly and without the need to test to see if everything is in working order. Ideally, a company’s testing equipment should be identical to what is being used by their motor repair facility, so that data can be trusted and fluid, or even better, shared digitally, enabling historical trends to be established. Another common issue is when a spare motor lies unused for a lengthy period, moisture and vibration can damage stator insulation and ball bearings resulting in a rise in infant mortality failure.
- Trending. The collection of test data on motors, taken on a regular, consistent basis provides companies with valuable information. By analyzing data trends, potential failures can be discovered early in the P-F curve. It is not enough to have equipment that can measure important data points; companies also need to invest in training or hiring qualified individuals who can spot irregularities in the trends in the data. Too often technicians function only as test-takers and miss small anomalies in data due to this knowledge gap, choosing to rely on the testing machine to alert them when something runs outside expected parameters.
Troubleshooting. When a motor shows signs of malfunction, troubleshooting allows technicians to diagnose and fix the problem quickly. The gap in this area occurs when companies do not have a detailed troubleshooting plan. A well-developed plan should include vendors, who are often a great resource even before troubleshooting is needed since they often know what potential problems may occur with a component. A good troubleshooting plan seeks to minimize downtime and help pinpoint root causes so they can be addressed as quickly and efficiently as possible. A comprehensive plan is also useful for identifying which root causes can be addressed at the factory and which require hiring cranes and moving the assets to a specialized repair facility.
The primary goal of identifying where these gaps are most likely to occur is to help ensure any existing problems are fixed before they become costly repairs. This is also another area where a reactive maintenance system shows some flaws regarding expensive assets, since often what drives the decisions is a short-term plan for profitability versus a longer, 20-year outlook, which is well within the potential life that an electric motor can be expected to last with a good predictive maintenance program.
Reliability vs. Supply Chain Shortages
With so much uncertainty shrouding the supply chain in Q4 of 2021 and early 2022, maintaining reliable means of production is even more paramount. When repair parts become scarce, the best investment a company can make is ensuring their existing equipment runs for as long as possible before breaking. Investing in reliability is a smart target for companies moving forward, even without a catastrophe looming in the background—and the primary issue that has caused the supply chain issues is far from resolved. Even when the present COVID-19 crisis has been resolved, taking a stance that mitigates the need for a constant flow of repair parts is the best insurance against any future crisis that may emerge.
About the Author:
Noah Bethel is vice president of product development for PdMA Corporation, Tampa, FL, the leader in the field of predictive maintenance, condition monitoring applications, and development of electric motor test equipment for motor circuit analysis. Tel: (800) 476-6463 or www.pdma.com.
- “Why the Pandemic Has Disrupted Supply Chains.” https://www.whitehouse.gov/cea/blog/2021/06/17/why-the-pandemic-has-disrupted-supply-chains/
- "We’re hoping that within the first six months of 2022, the port situation and efforts to increase capacity, both on the railroad and trucking, will improve substantially. If that happens and the demand on the system lessens, things will look better by summer," Panos Kouvelis, director of The Boeing Center for Supply Chain Innovation at Washington University in St. Louis. https://phys.org/news/2021-11-chain-disruptions.html
- According to an international survey conducted by Zurich Insurance and the Business Continuity Institute during 2018-2019. https://www.supplychainquarterly.com/articles/3152-seven-steps-to-counter-catastrophe
- A comprehensive overview of how PdMA approaches the six fault zones for predictive maintenance. https://pdma.com/pdfs/Articles/Using_a_Six_Fault_Zone_Approach_for_Predictive_Maintenance_on_Motors.pdf
- See also “Using a Six Fault Zone Approach for Predictive Maintenance on Motors” https://pdma.com/pdfs/Articles/Using_a_Six_Fault_Zone_Approach_for_Predictive_Maintenance_on_Motors.pdf
- A more in-depth article about these gaps. https://pdma.com/2021/01/08/gaps-in-your-electric-motor-reliability-program/
Advertisement