Infrared Inspections of Lightning Arrestors
Sponsored by:
Tip written by: Infraspection Institute
Infrared thermography is a proven technology for detecting defects in electrical circuits that are under load. Thermal imaging can also be used to detect defective lightning arrestors that are leaking current to ground.
Lightning arrestors are a common feature in electrical distribution systems and are used to guard against voltage surges associated with lightning strikes on power or communications lines. Installed at strategic locations, lightning arrestors act like safety valves to provide a short circuit path that carries excess voltage to ground during a lightning strike.
Lightning arrestors are connected between a conductor and ground. In order to prevent a ground fault, lightning arrestors are engineered so that normal line voltage will not pass through the arrestor under normal conditions. While some lightning arrestors employ a simple spark gap, others consist of porcelain tubes that are filled with semi-conductive discs made of silicon carbide or zinc oxide. During a lightning strike, the resistance of the spark gap or oxide plates is overcome and excess energy flows to ground.
If a lightning strike is sufficiently strong, lightning arrestors may be permanently damaged and begin to conduct electricity to ground full time. When this happens, the body of the arrestors will heat up allowing them to be detected with a thermal imager. The images below show two examples of defective arrestors.
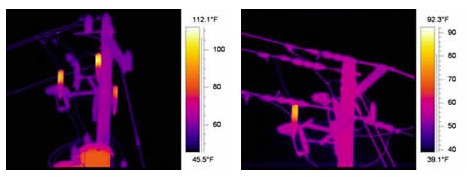
~ Images courtesy Stockton Infrared Thermographic Services
Infrared inspections of lightning arrestors are primarily qualitative in nature. As such, thermographers should compare similar arrestors to one another and note any that are inexplicably warm.
Properly functioning lightning arrestors should be uniform in temperature and close to ambient air temperature if they have not undergone recent solar loading. Individual arrestors should not have any pronounced hot spots across them. Working early in the morning, on cloudy days or at night will help to eliminate solar loading which can hide defective arrestors. When performing your inspection, don’t forget to check grounding connections for hot spots as well.
Infrared inspection of power distribution systems is one of the many topics covered in the Level I Infraspection Institute Certified Infrared Thermographer® training course. For information on thermographer training including course locations and dates, visit us online at www.infraspection.com or call us at 609-239-4788.
Advertisement