Scheduling IR Equipment for Maintenance
Sponsored by: Infraspection
Many thermographers think of the holidays as a time for family, festivities and annual maintenance of their infrared equipment. Planning ahead can help to minimize imager downtime and avoid or minimize program interruption.
Because infrared test equipment plays a key role in an inspection program, minimizing downtime required for service is imperative. Keeping the following in mind can help routine service to proceed more smoothly and ensure a faster turnaround for your imager.
- Schedule routine equipment service and/or calibrations well in advance
- Most service departments require you to obtain a Return Authorization before shipping equipment
- Be sure to include all optics and filters when shipping your system
- Consider scheduling service before or after holidays to avoid service backlogs
- Arrange for replacement equipment if you anticipate a long delivery time for service
When shipping your equipment, enclose a letter stating services required and any problems with the subject equipment. Be sure to affix a Packing List to the exterior of your shipping container noting descriptions and serial numbers of items shipped. Lastly, don’t forget to ascertain Customs requirements if your equipment must be shipped outside of your country for service.
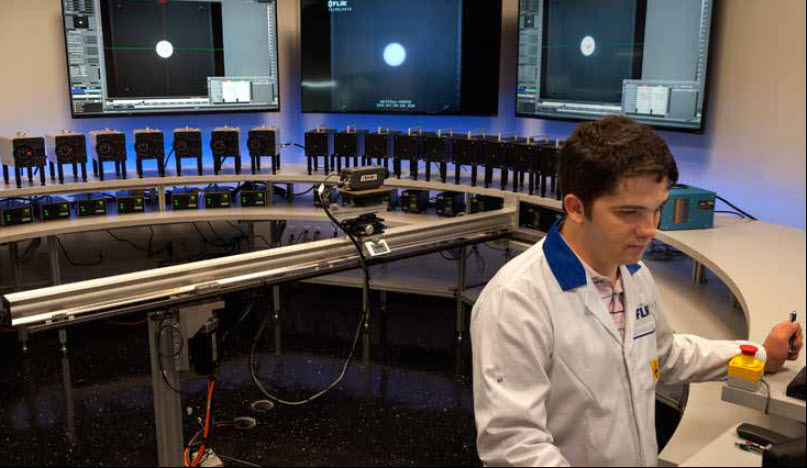
Infrared equipment selection and operation are two of the many topics covered in all Level I Infraspection Institute Certified Infrared Thermographer® training courses. Level I training is available at several locations each month and through our Distance Learning Program. For information on thermographer training including course locations and dates, visit us online at www.infraspection.com or call us at 609-239-4788.
Advertisement