Adrian Messer
Manager of US Operations
UE Systems, Inc.
Ph: 864-224-4517 Cell: 914-282-3504 www.uesystems.comAbstract
When it comes to establishing an electrical maintenance program for your facility, there are many resources at your disposal to which you could look. As for the tools that can be used to then inspect energized electrical equipment, an infrared camera is probably the first tool that comes to mind. Some of you may have even said an airborne ultrasound instrument. If you said ultrasound, you are among a growing number of maintenance and reliability professionals who have come to realize that airborne ultrasound is a viable tool that can effectively be used to inspect and diagnose conditions such as corona, tracking, arcing, and partial discharge in energized electrical equipment.
The standards that maintenance and reliability professionals have access to for guidance when establishing procedures and best practices for inspecting and maintaining electrical equipment in facilities are the National Fire Protection Association (NFPA) 70B, and the Canadian version the Canadian Standards Association (CSA) Z463. Both of these documents have been established in order to create recommended practices for inspecting and maintaining electrical assets in order to prevent accidents and reduce downtime.
Discussion
NFPA 70B & CSA Z463
According to NFPA 70B standard for electrical maintenance, an Electrical Preventive Maintenance program is “a managed program of inspecting, testing, analyzing, and servicing electrical systems and equipment with the purpose of maintaining safe operations and production by reducing or eliminating system interruptions, and equipment breakdowns”.
When it comes to the inspection tools that NFPA 70B recommends for inspecting energized electrical equipment, the document only mentions ultrasound in two sections. The first mention is in section 11.21.3.3.2.2 when discussing partial discharge. The other mention is in section 15.1.2.2 which discusses corona in substations and switchgear.
The Canadian equivalent to NFPA 70B, the CSA Z463, goes into more detail when discussing ultrasound technology. CSA 463 says in section 7.10.2 that “ultrasound inspections use collectors that detect the high frequency produced by the emissions caused by electrical arcing, tracking, and corona.” This section also goes on to mention the fact that the sound heard by the inspector can be recorded and then further analyzed in a spectrum analysis software for an accurate diagnosis of what was detected by the ultrasound instrument.
As for airborne ultrasound, a technology that was once considered just a leak detector, users of the technology quickly began to realize that the instruments could be used for other applications, such as condition monitoring of rotating equipment and electrical inspection. To many, airborne ultrasound has become a necessity when inspecting energized electrical equipment. The primary driver of this application is safety. In most cases, airborne ultrasound inspection can be done without opening energized electrical cabinets. Performing an inspection without opening energized electrical equipment helps to reduce the risk the inspector faces from potential exposure to arc flash hazards.
What is Ultrasound?
Ultrasonic equipment detects airborne and structure-borne ultrasounds normally inaudible to the human ear and electronically “transposes” them into audible signals that a technician can hear through headphones and view on a display panel as a dB level. On some instruments, incoming sound can also be viewed on a spectral analysis screen which shows either the FFT or Time Wave Form. With this information, a trained technician can interpret the bearing condition in order to determine what, if any, corrective action is needed, and the current data can be compared on the spot to the baseline data.
Ultrasound technology has many advantages:
- It can be used in virtually any environment.
- Learning to use ultrasound technology is relatively easy.
- The technology is relatively inexpensive.
- Modern ultrasonic equipment makes it easy to track trends and store historical data
- Ultrasonic technology has proven itself to be extremely reliable in predictive maintenance, saving thousands upon thousands of dollars and hours of lost productivity
- There are remote monitoring options for both mechanical and electrical applications
Airborne and structure-borne ultrasound instruments are an extension of the user’s sense of hearing. Similar in that vibration feels what you can’t feel and infrared cameras see what you can’t see, ultrasound hears what you can’t hear. There are sounds taking place in a typical plant and manufacturing environment (machines running, production equipment running, etc.) that prevent us from hearing other sounds such as compressed air leaks, or electrical discharges like corona, tracking, or arcing. Ultrasound instruments listen for sounds that are not present in our normal audible range.
Typically, the sounds outside normal human hearing are high frequency sounds. The high frequency sounds are detected by the instrument and translated through a process called heterodyning into an audible sound that is heard in the headset by the inspector. The unit of measurement for sound is a dB level which is indicated on the display of the ultrasound instrument.
The ultrasound inspection can be done by scanning any openings on the cabinet itself, such as vent opening, seals around doors, louvers, etc. Therefore, before any energized electrical cabinet is opened for maintenance or further inspection, a pre- inspection can be done with ultrasound to see if any anomaly is heard. If there is a condition like corona, tracking, or arcing inside of the electrical equipment, the ultrasound produced by those anomalies will be heard by the inspector via those openings. The source of the ultrasound produced is ionization.
Electrical Inspection with Ultrasound
Ultrasound can be used to inspect almost any energized electrical equipment. This equipment may include metal-clad switchgear, transformers, substations, relays, and motor control centers, along with many others. Ultrasound can be used to measure equipment voltages from the low end (110 volts) to well over 12000 volts (12kV).
Traditionally, inspection of energized electrical equipment has been performed using noncontact infrared cameras. However, in recent years, ultrasound has been added to these inspections for various reasons. One of the main reasons has been for safety: An ultrasound inspection of electrical equipment can be done without the need to open the energized cabinet or enclosure. The hand-held ultrasound instrument is used to scan any openings on the cabinet. The high frequency sound produced by corona, tracking, and arcing from inside of the enclosure will exit through any of the openings. The inspector will hear the sound via the headset, and know that an anomaly is present.
The sound can then be recorded to determine if the condition is corona, tracking, arcing, or some type of mechanical looseness.
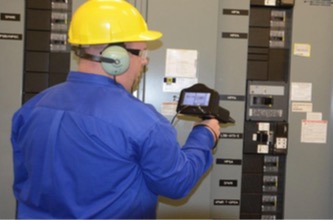
Corona refers to the ionization of air surrounding an electrical connection above 1000 volts. Corona, by nature, does not produce significant heat that would be detected by an infrared camera. However, it does produce high frequency sound that can be detected by the ultrasound instrument. If corona discharge continues to occur, it can lead to a more severe problem such as tracking or arcing. Byproducts of the ionization process are ozone, electromagnetic emissions, ultraviolet light, and nitric acid. The nitric acid is a corrosive and can deteriorate the insulators and connectors and lead to tracking and arcing.
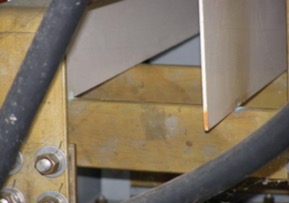
board resting on 13kV bus. Notice the carbon deposits and light
brown discoloration of the insulation board on the right.
When the sound file of corona is recorded, there are signature characteristics visible in the FFT and Time Wave Form (TWF) that will help to diagnose the condition. For corona, the discharge points only occur at the highest voltage point on the sine wave. This means that the amplitude peaks in the TWF are somewhat equally spaced as the discharges are only at the positive peak of the sine wave. The result will be well defined 60Hz or 50Hz harmonics.
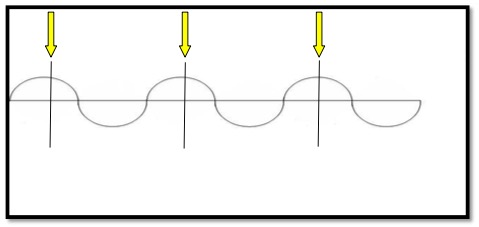
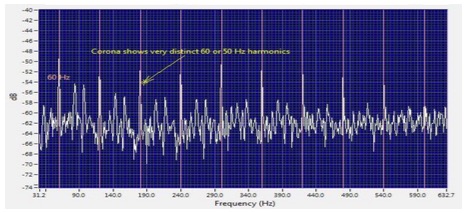
For tracking (low current pathway to ground across an insulator) and arcing (electrical discharge to ground across an insulator) there are also certain characteristics to look for. With tracking, the discharge does not have to take place at the peak of the waveform. Instead, it can happen anywhere on the positive portion of the cycle. The spacing of the peaks in the TWF would be similar, but not uniform. As tracking becomes more severe, there are more discharge events and therefore more non- uniformly spaced narrow peaks.
Arcing has the most non-uniform “look” in the FFT and TWF. Only the bursts of the discharge can be heard and these will be seen as wide peaks in the TWF view.
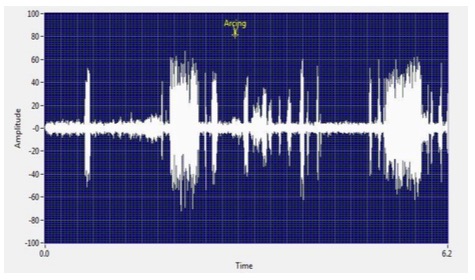
Conclusion
As for NFPA 70B, in all fairness, we are currently in the middle of a revision period for the standard. The next revision is scheduled to be released in 2016. I hope that the 2016 revision of NFPA 70B will add additional information regarding ultrasound, and how it can be used for electrical inspections. Both documents do go into great detail regarding the inspection and maintenance of any electrical asset in a facility. There are even recommended procedures discussed regarding asset criticality and establishing an electrical maintenance program.
If you happened to be on the Technical Committee for NFPA 70B, I would welcome any comments and discussions regarding airborne ultrasound technology and its uses for inspecting energized electrical equipment. Speaking from experience, I can vouch for the fact that there is certainly an increased interest in airborne ultrasound for electrical inspection, not only from maintenance and reliability professionals in plants and facilities, but also from insurance companies that inspect a facility’s electrical infrastructure.
Sources:
www.nfpa.org NFPA 70B
www.csa.ca CSA Z463