Jay Ray – Founding member of IFSPA
and R. Olsen
Maine Infrared Solutions
40 Orchard Lane
Otisfield, ME 04270
207-749-2741Abstract
I have been in the window and door troubleshooting industry for thirteen years and I am very excited about a new tool that I added to my arsenal this year. Statistics show that in New England, 98% of water invasion and cold air infiltration in windows and doors is attributed to improper installation. Infrared thermography allows me to find problems and validate my diagnoses. What is really important is that the IR images can be read and understood by window and door manufacturers, dealers, contractors, and even homeowners. Best of all, it can lead to a solution that is the most cost-effective for that particular situation.
It is not uncommon in the industry to replace every window in a home due to a small shortcoming in the installation method or a small manufacturing defect. Misdiagnosis of a problem can cost the manufacturer, reflect badly on the factory and the dealer, cost the contractor time, and importantly, add unnecessary aggravation for the homeowner. My thermal camera has become the most valued tool in my truck. When I use the camera and find a problem, or the extent of a problem, everybody wins! This paper shows examples of what I have found and how I have saved money for all parties involved.
Discussion
Errors in Installation
Errors in the systematic process of installing a window or door can lead to air and water infiltration as well as poor operation, and can substantially shorten the service life of the product.
No matter what climate you are in, from New England where the winters are brutally cold and wet, to the Southeast where the summers are equally warm, humid and wet, or to the extreme heat of the desert Southwest, a poor installation wastes money in excess heating and cooling costs. Installation of door and window products according to the manufacturers specifications for a particular location and environment, is the most desirable method and should be followed to the letter to ensure that the door or window meets or exceeds the performance level of that product.
Poor operation is usually the fault of the installer and there is no technology better than the human eye, ear, and hand to determine what the problem is and how it is to be repaired.
For issues of air infiltration, a smoke pencil, in addition to the human hand, is the preferred method of investigation.
When it comes to water infiltration or intrusion, as we like to call it, the human eye is good and has been forever – but there is absolutely no better technology to find the source and path of this intrusion than infrared thermography.
Use of Infrared in Finding Installation Problems
An initial, non-certified, non-calibrated water test using a garden hose is, in most cases, all that is needed to find the problem.
Other times, a blower door is employed in addition to the above water test to create a negative interior pressure similar to a storm.
For years, we have represented the window and door manufacturers and our prime concern was water entering through the unit. When a unit leaks when it is not supposed to, the manufacturer is held responsible in the eye of the homeowner.
This is easy to discover and the repair / remediation process is standardized by the factory. The thermogram that follows shows a glazing juncture failure where water is coming around the bottom of the insulated glass unit (IG) on a door.
In instances where we believe the water intrusion is around the unit as a result of poor installation and not the fault of the product itself, we have had to resort to the destruction of the interior surface to see the exterior wall assembly and window/door frame to prove this visually, and document it using a simple moisture meter.
Infrared thermography makes the process very simple. We only have to look where we see a thermal anomaly typical of water intrusion around or under the subject unit.
The ability to document what we find with a thermogram is crucial to getting the problem resolved by the correct party.
The issue of air infiltration is one where the human hand is the best tool for discovery. Many times, a homeowner or builder will complain that a “seal failure” is causing a draft. This is impossible. In a cold climate, they are likely to sense a “thermal draft” where the warm air at the ceiling is naturally cooling, and as it drops across the face of the fenestration unit, the glass acts as a heat sink with the air losing heat rapidly, causing the sensation of a drafty window.
A true “seal failure” has very little impact on building heat loss or gain. An Insulated Glass unit (IG) was originally designed for the intent of reducing, and hopefully eliminating, interior condensation on the glass, which led to degradation of the wood fibers (wood-rot) in a wood frame window.
An IG unit creates a “dead-air” space, not a vacuum, between the glass panes, which allows the indoor ambient temperature to keep the interior surface of the glass above the dew point. Prior to IG units becoming available in commercially available residential window units, a storm window was employed.
IG units allowed the use of casement and awning windows where a storm window could not be previously employed. A storm window, when installed properly, creates a near-dead air space between the actual window and the outside. This near-dead air space essentially creates a situation close to that of an IG, where convection currents are substantially immobilized.
The spacer of an IG is the only place that conductive heat loss or gain can occur. The only place on an IG unit where infrared thermography can be of use is observing and recording the heat transfer at and near the IG spacer.
The most significant areas of heat loss/gain on any fenestration unit are where the operable sash meets the unit frame employing weather-seals, and around the unit itself where it is attached to the building. More heat is lost at these places of a window than at the glazing. Also, heat loss/transfer at the exposed glazing surface is unavoidable.
The use of infrared thermography in assessing the performance of a window is easy. With a Delta-T present in a static air pressure environment, the natural convection and conduction of heat transfer through and around the fenestration unit can be imaged both from the interior and the exterior. In a cold climate, such as Maine, if insulation is missing between the window unit and the rough opening, a thermal anomaly will be present.
The unit above was found to have a void in the insulation at the bottom of the rough opening. The initial scan showed a cold anomaly and removal of the casing proved this.
Using a blower door to simulate a constant 25 mph wind (interior air pressure – 50kPa), an interior infrared thermogram can accentuate the junctures or areas that need to be sealed and/or insulated where possible.
Visit out Sponsors:
Electrophysics
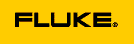

